Extreme Power and Stability for Heavy-Duty Machining
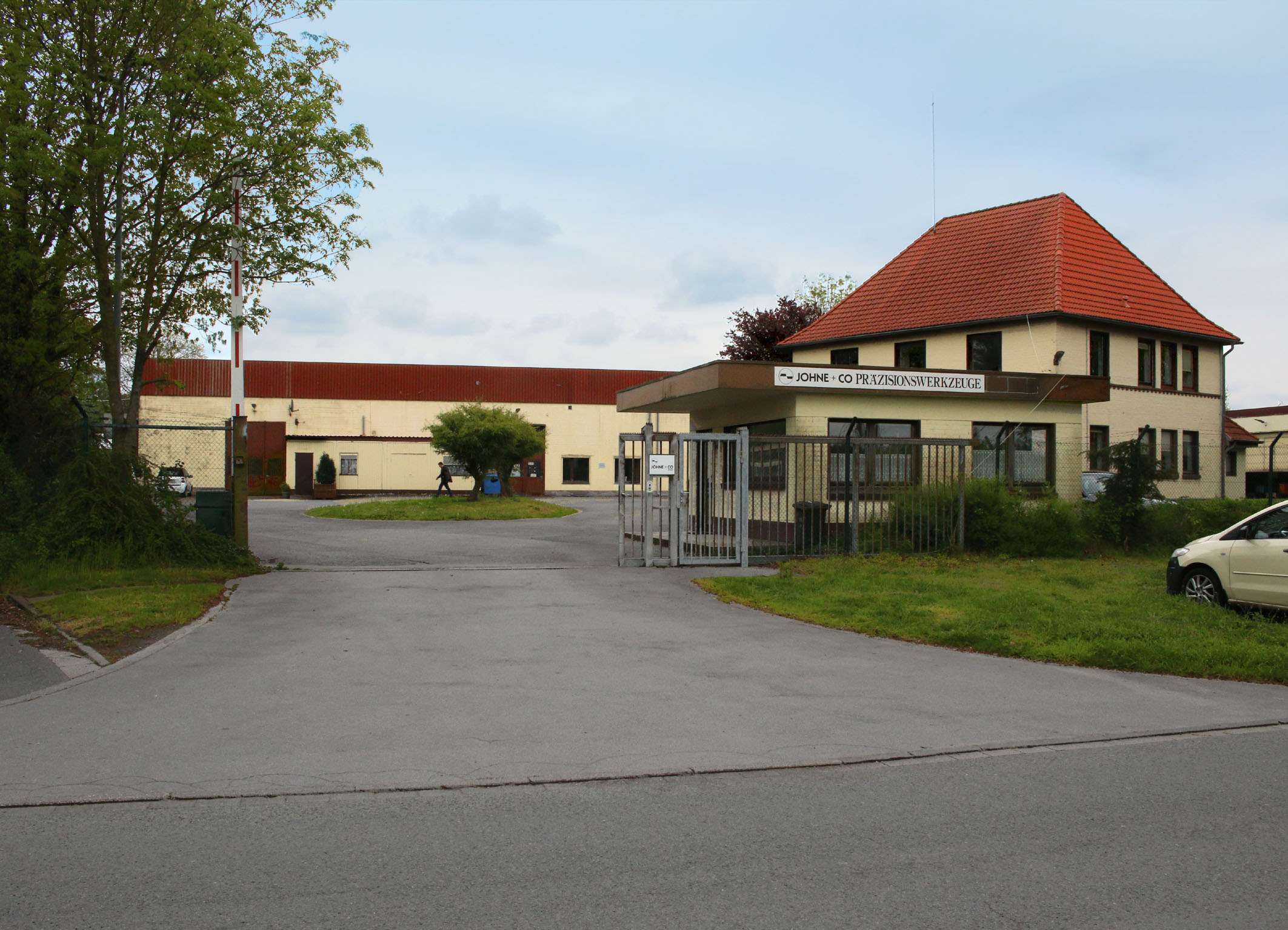
Contract manufacturing companies often process a wide range of parts in various batch sizes for their clients, ranging from small series to mass production. The size and complexity of workpieces also vary from order to order. Accordingly, the machine tools used in this field must offer a high degree of flexibility while maintaining high precision and repeatability. A subcontractor from southern Münsterland has recently been relying on a horizontal machining center with pallet changer from the leading South Korean machine tool manufacturer HWACHEON for the complete machining of workpieces with partly complex geometries.
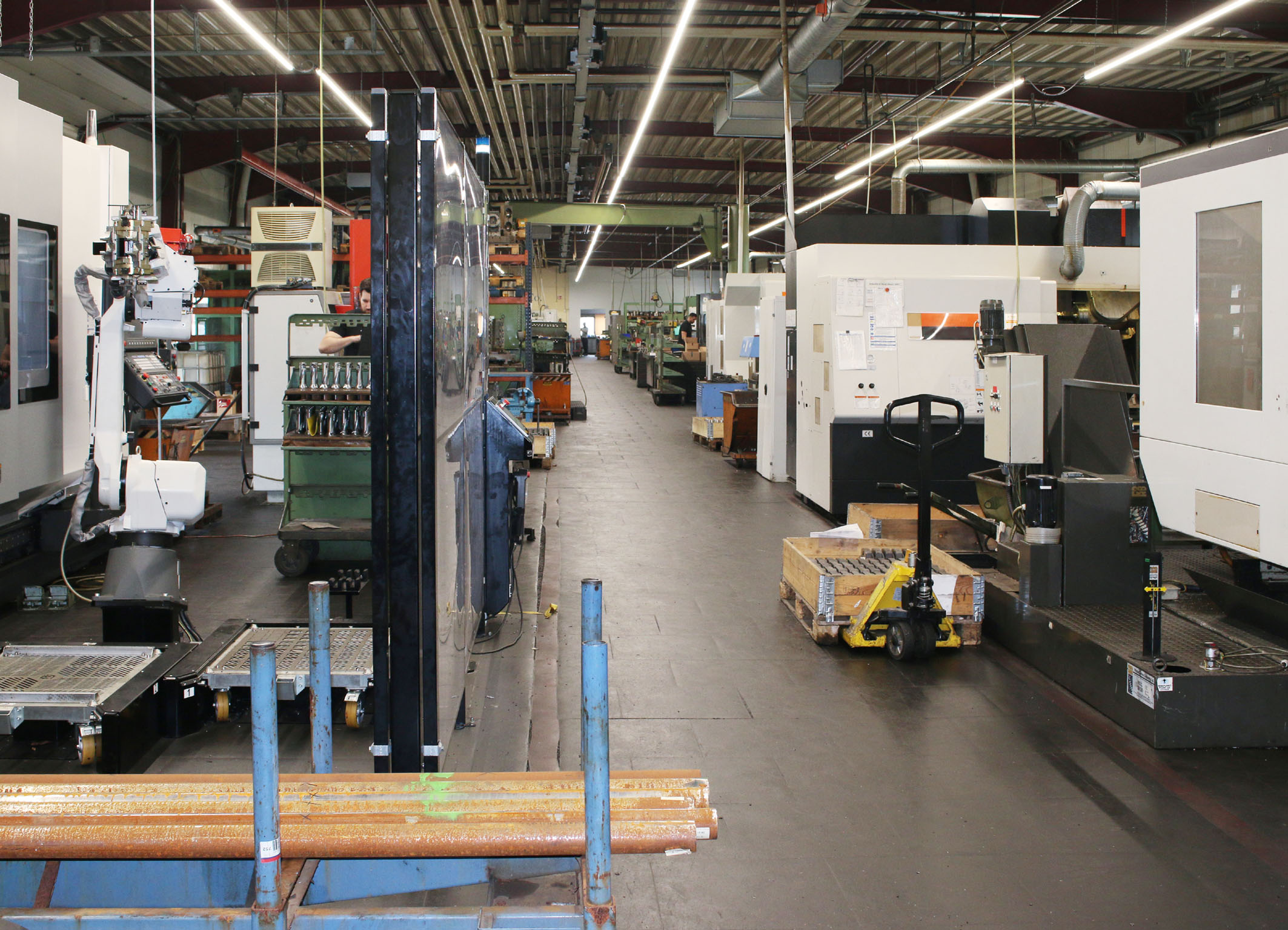
The second pillar is contract manufacturing, where the company can look back on 30 years of experience. A comprehensive machine park is available for this purpose, with which turning, milling, and grinding operations are performed on sometimes very complex parts. The clients come from various industries such as machinery, special machinery, textile machinery, and agricultural machinery manufacturing, automotive, railway and signaling technology, as well as heating and cooling technology. In recent decades, contract manufacturing at Johne has been continuously expanded. "Today, this area accounts for about 60 percent of our sales, while precision tools contribute 40 percent," explains Ludger Krampe, one of the partners of Johne & Co. Präzisionswerkzeuge GmbH. "In the early days, it was the exact opposite."
Batch Sizes from 1 to 20,000
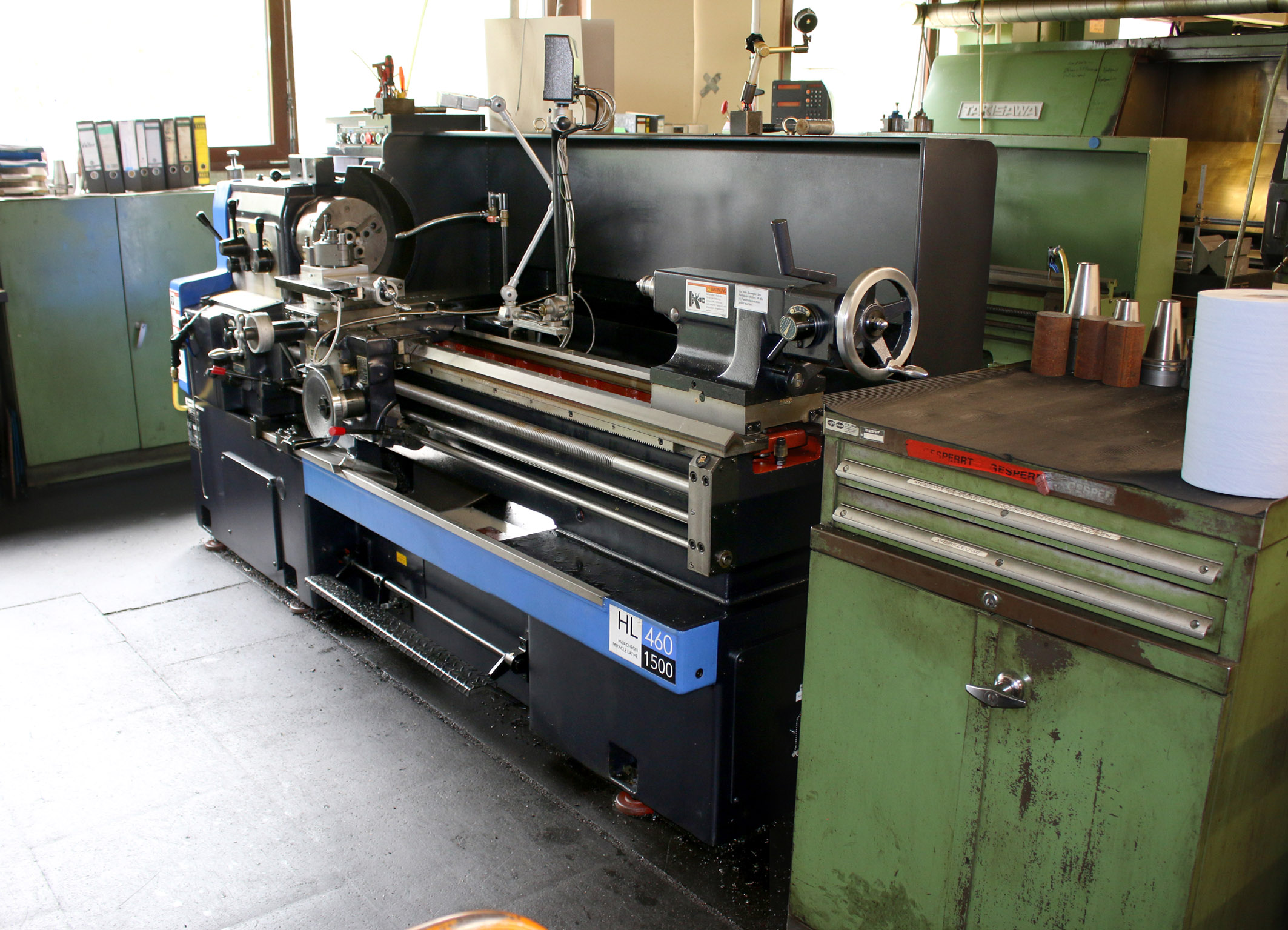
The company shows great flexibility in batch sizes: It offers the development and construction of prototypes from batch size 1. For precision tools, usually between one and 50 units are manufactured, while the number is between one and three for special tools. In contract manufacturing, the batches start at 20 units and can reach a batch size of 20,000 per month for a part for a special pump.
High-Quality Machine Package
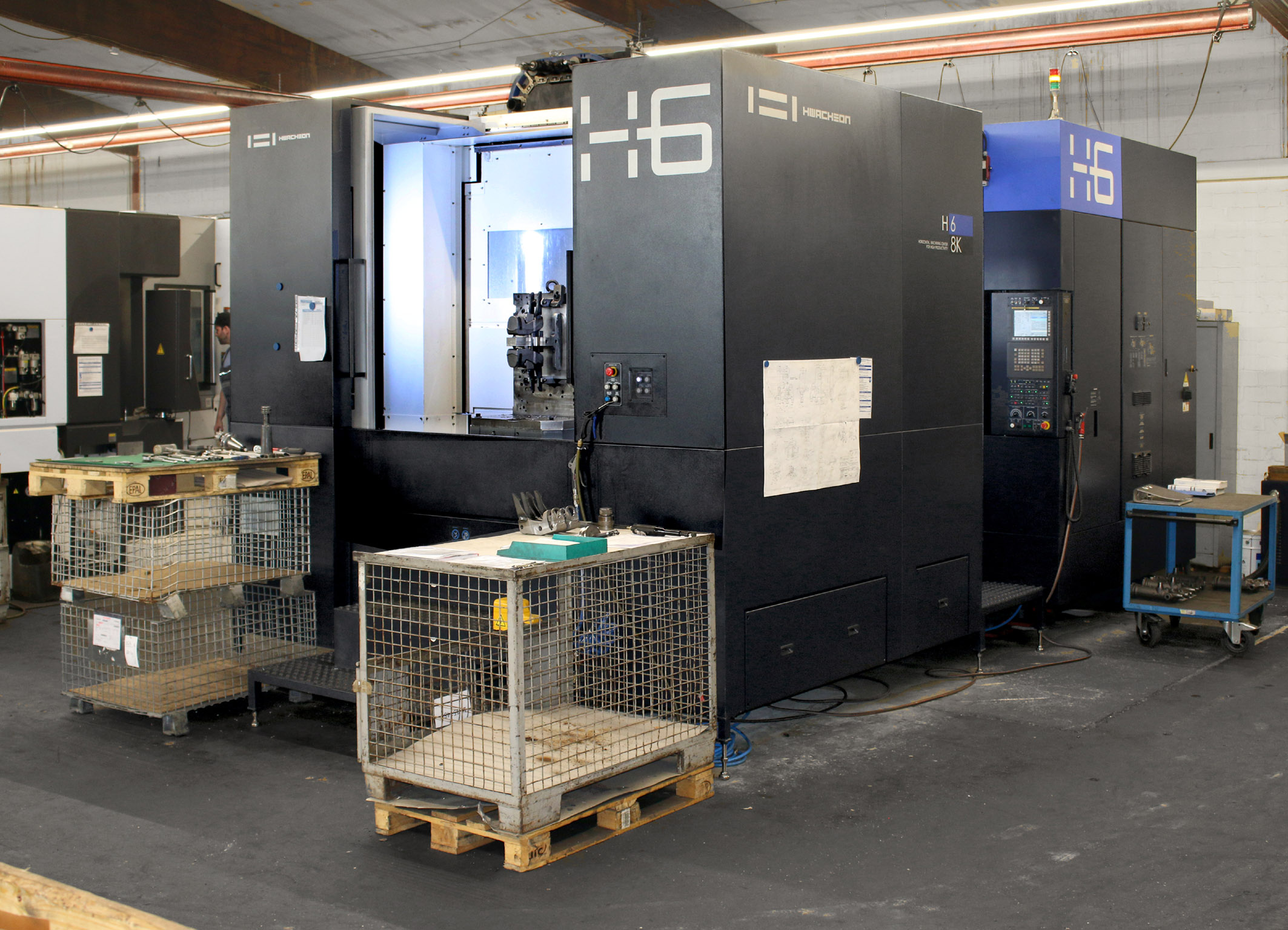
Quality assurance at Johne also includes the continuous modernization of the machine park. Additional machines are purchased if the space available in the two halls permits. Ludger Krampe was initially looking for a conventional lathe in 2018. A former self-employed service technician drew his attention to the South Korean-manufactured machine tools of his new employer. "I was already familiar with the HWACHEON brand from the time when they were still distributed in Germany through Hommel, but I hadn't dealt with the machines themselves at that time," Krampe recalls. That was to change quickly, as a machine package was arranged at the end of the decision-making process, which included a conventional lathe and a horizontal machining center with extensive equipment. This process was accompanied by the HWACHEON European headquarters in Bochum, through which customer service and fast spare parts supply are handled.
Machining Center with Broad Application Spectrum
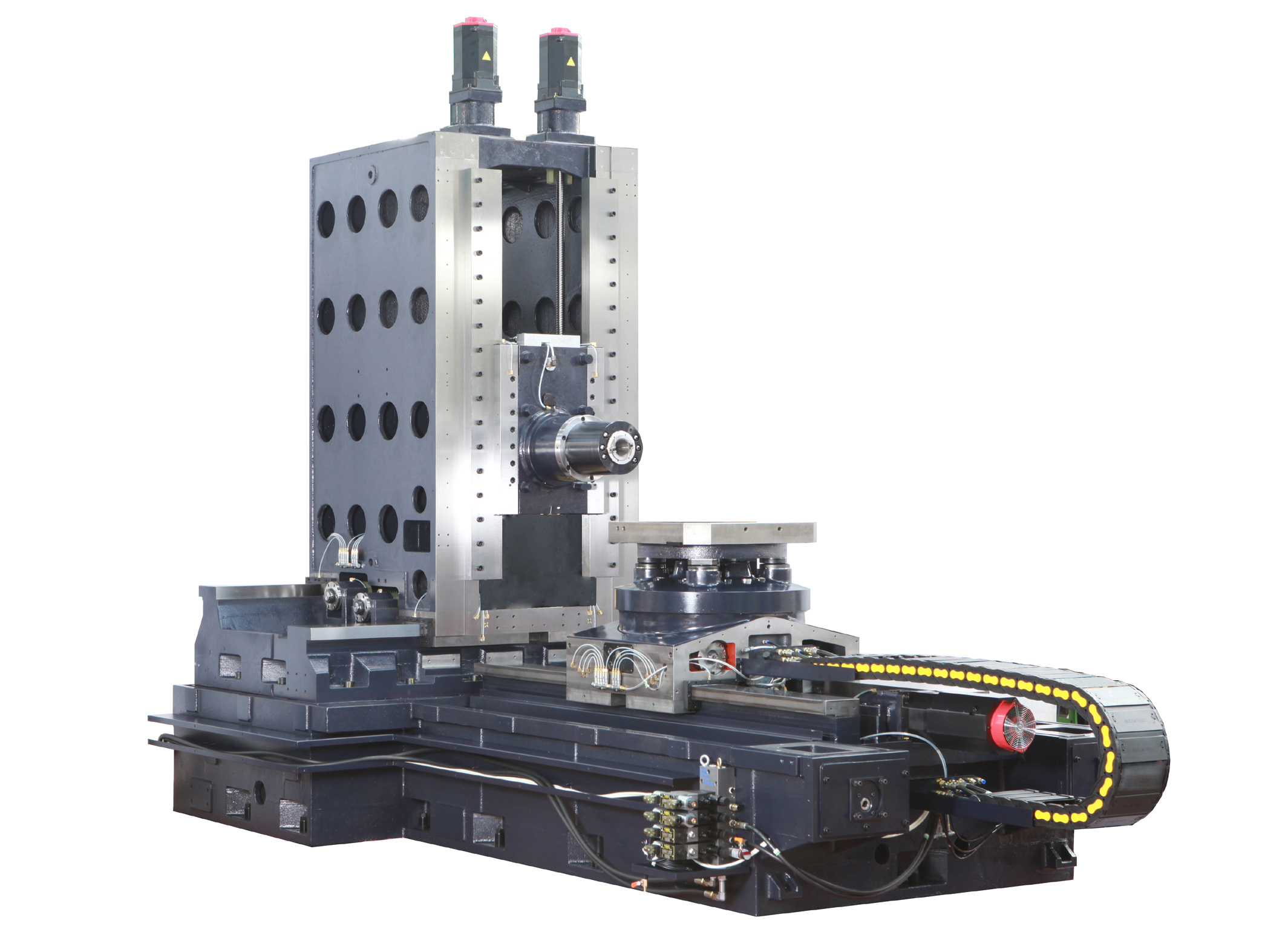
For heavy-duty machining of workpieces with partly complex geometries, Ludger Krampe was looking for a suitable machining center and became aware of the robust H-series from HWACHEON, which had just been introduced to the European market at that time. The targeted horizontal machining center HWACHEON H6 is particularly stable and powerful during roughing, while also allowing precise and dynamic finishing. Like its bigger sister H8, it opens up a wide range of applications, from series production of hard-to-machine precision parts to achieving high surface quality in tool and mold making.
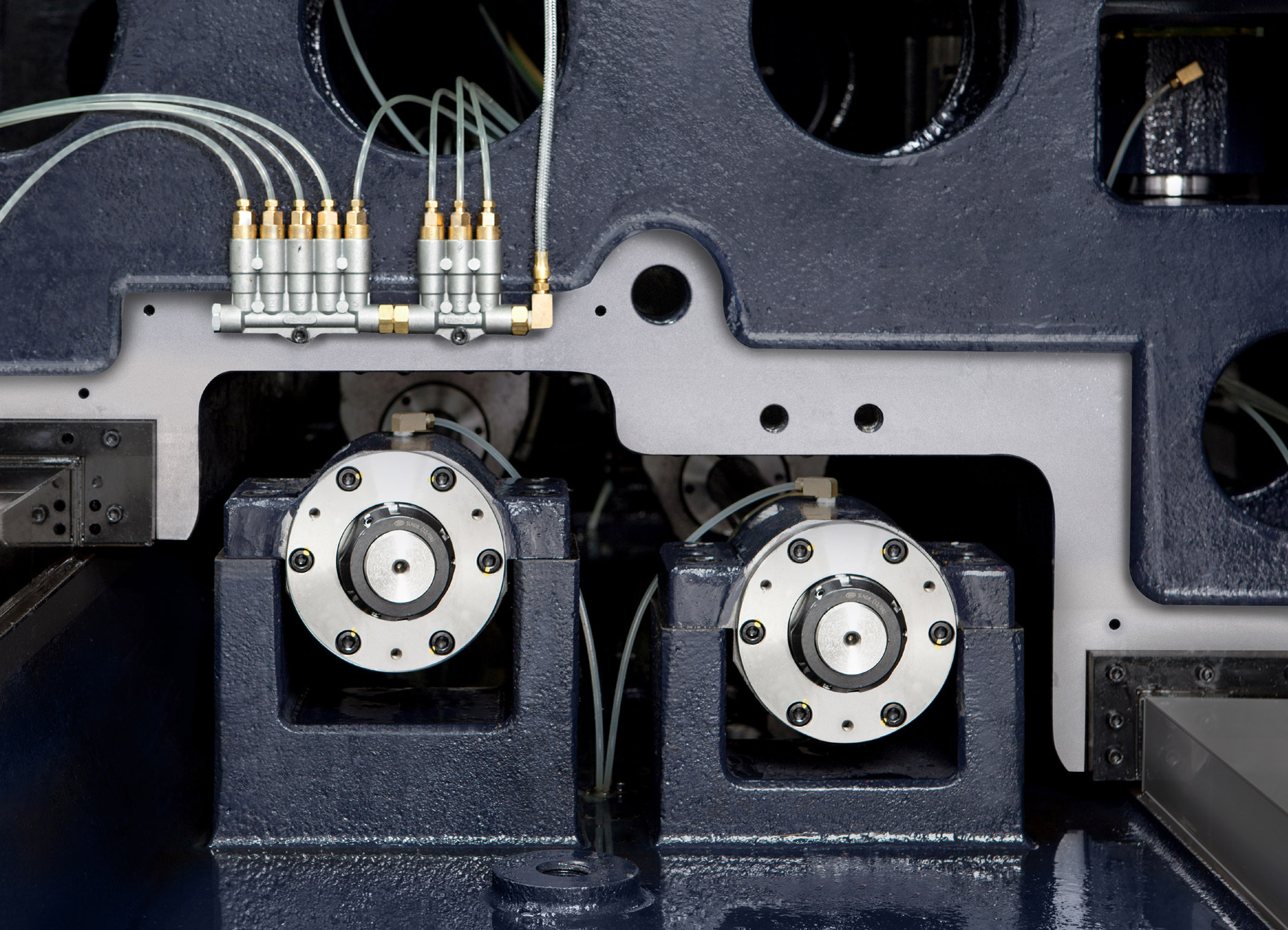
This is mainly made possible by the high weight of the H6 of 26.5 tons and the massive and extremely rigid structure of the machine bed and stand. The T-shaped bed is made of Meehanite cast iron and is thermosymmetrically constructed to ensure dimensional stability throughout the entire process, even during long and chip-intensive work operations. The generously dimensioned and hand-scraped flat guides, as well as the twin drives in the X and Y axes, allow precise and high cutting rates. Pneumatically pressurized flat guides result in low breakaway torque and guarantee uniform movements at rapid traverses up to 48 m/min.
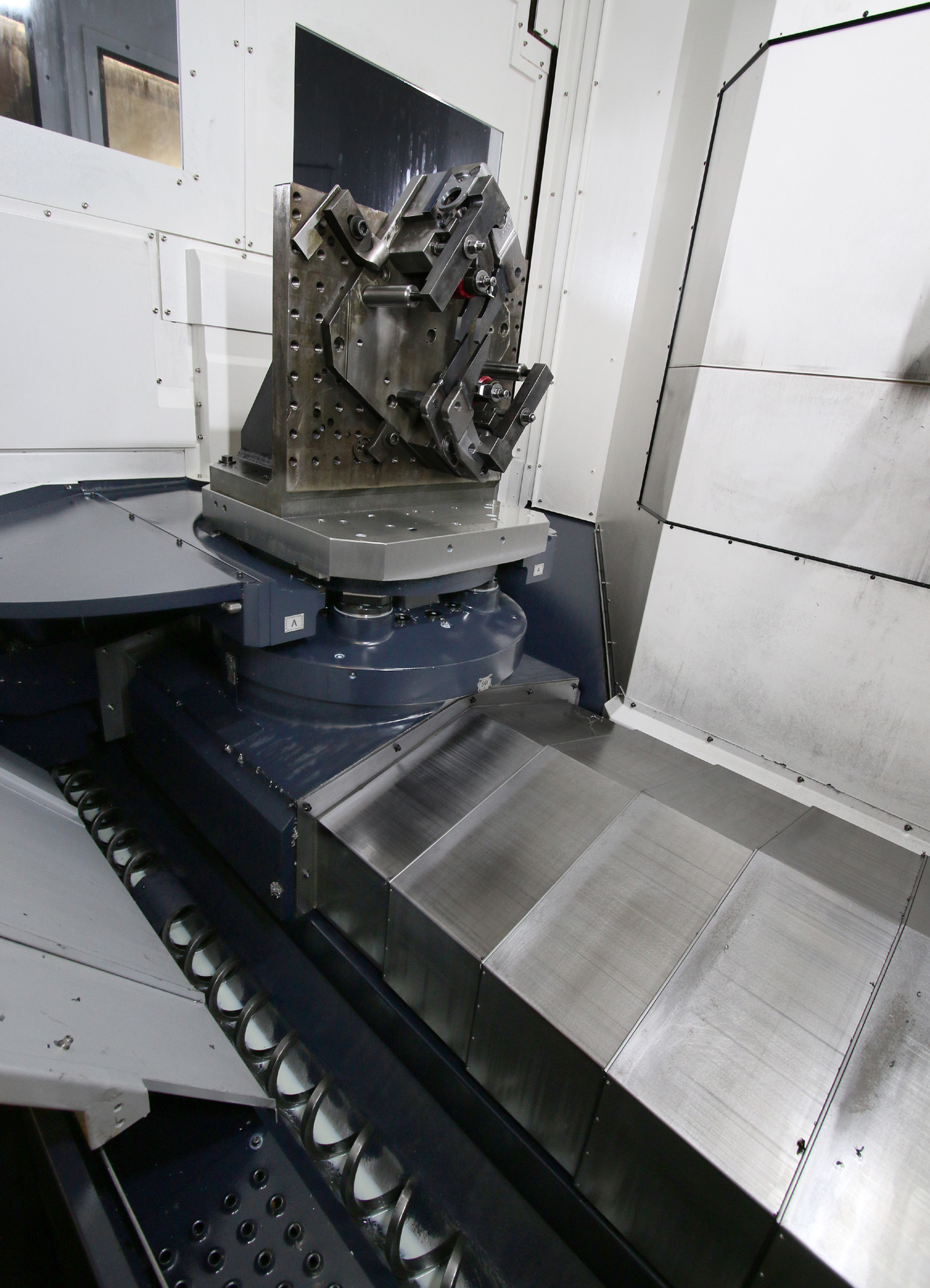
For economical series production, the H6 is standardly equipped with a pallet changer and two pallets in the 630 x 630 mm format. The backlash-free preloaded worm gear of the simultaneously controlled B-axis, in conjunction with the directly controlled encoder, ensures compliance with accuracy requirements.
A Lot of Power and High Torque
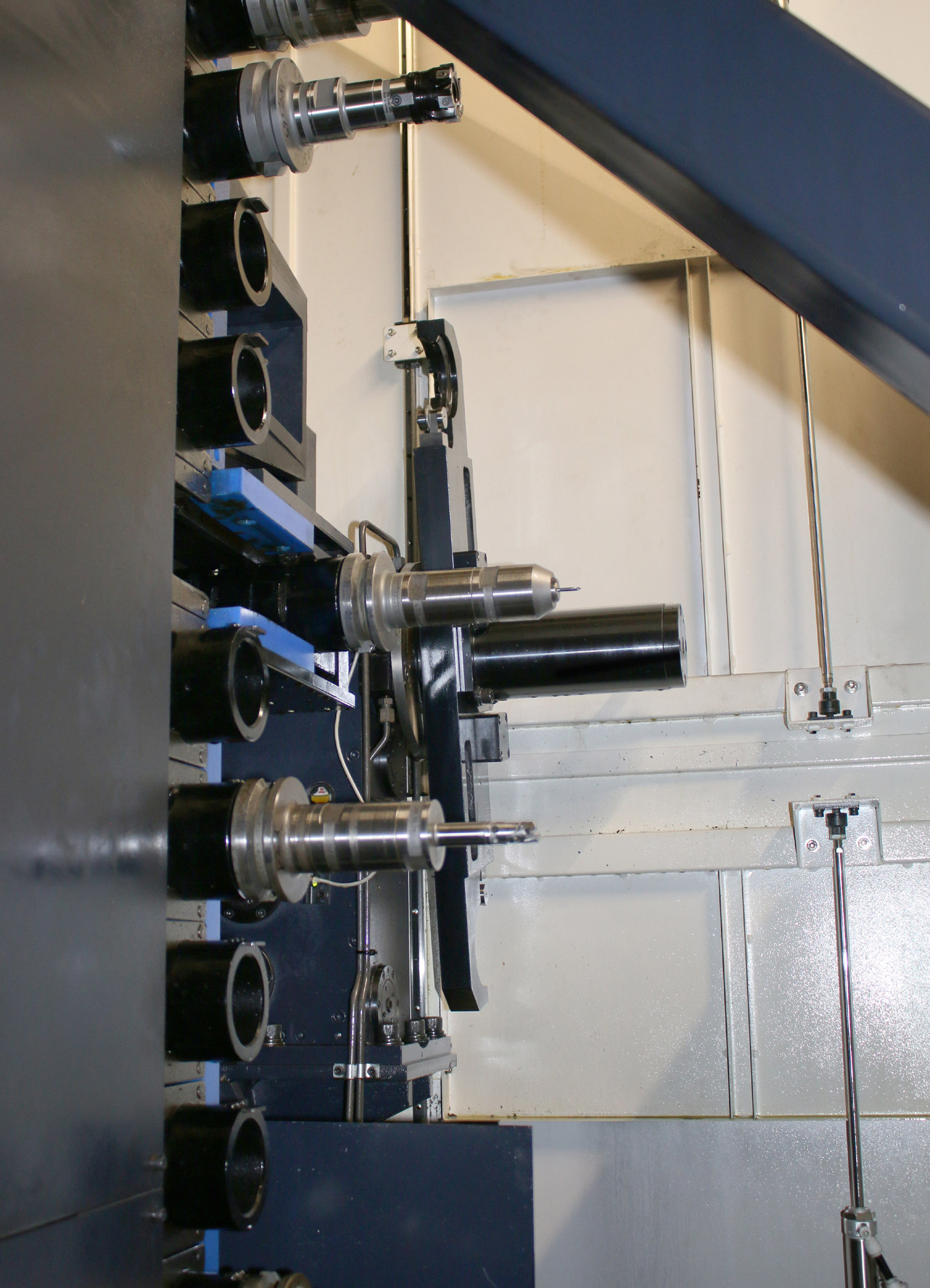
In configuring the machining center, the Johne partner could choose between different options. Thus, it is optionally available with a Fanuc 31i or Siemens 840D control, with the decision being made in favor of the Fanuc control in this case. There were also two options for the spindle: a motor spindle with 12,000 rpm or a gear spindle. “Since we also process super duplex steels on the machine, we needed a spindle with a lot of power and high torque,” says Ludger Krampe. “Therefore, we decided on the gear spindle.” This comes from HWACHEON's own spindle production and is designed as a two-stage model with an output of 35 and 22 kW, respectively. At 8,000 rpm, it offers a torque of 1,654 Nm, thus effortlessly fulfilling all the requirements of heavy-duty machining.
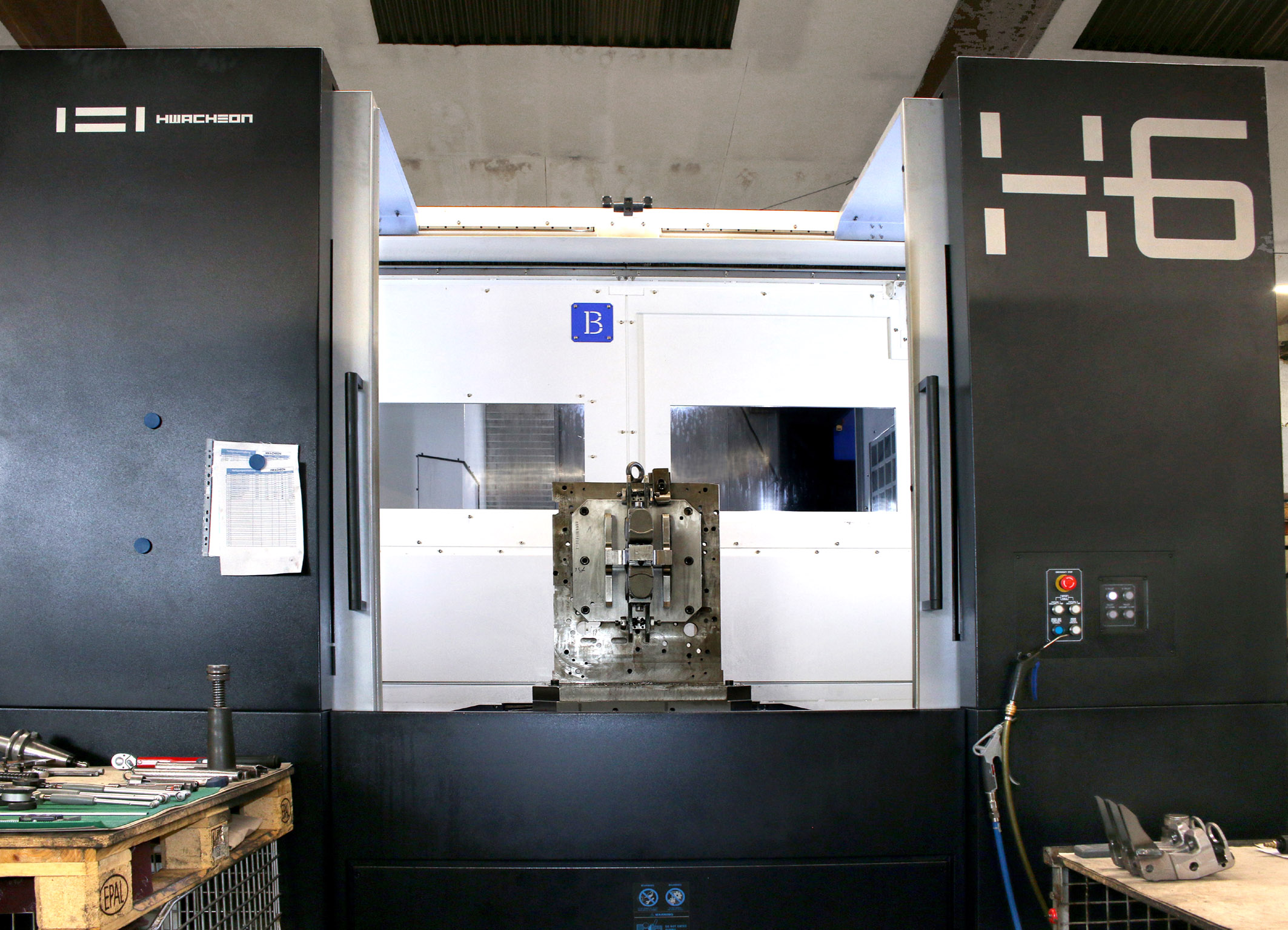
The tool magazine of the machine selected by Johne offers 60 spaces, providing essentially sufficient capacity for the machining of complex workpieces with numerous tools. “However, for us, a few more would have been possible,” Krampe smiles. “After all, we already need 20 to 25 tools for machining a workpiece.” These include, in addition to roughing and finishing tools, drills of different diameters, taps, and, of course, fine-boring solutions that come from in-house production.
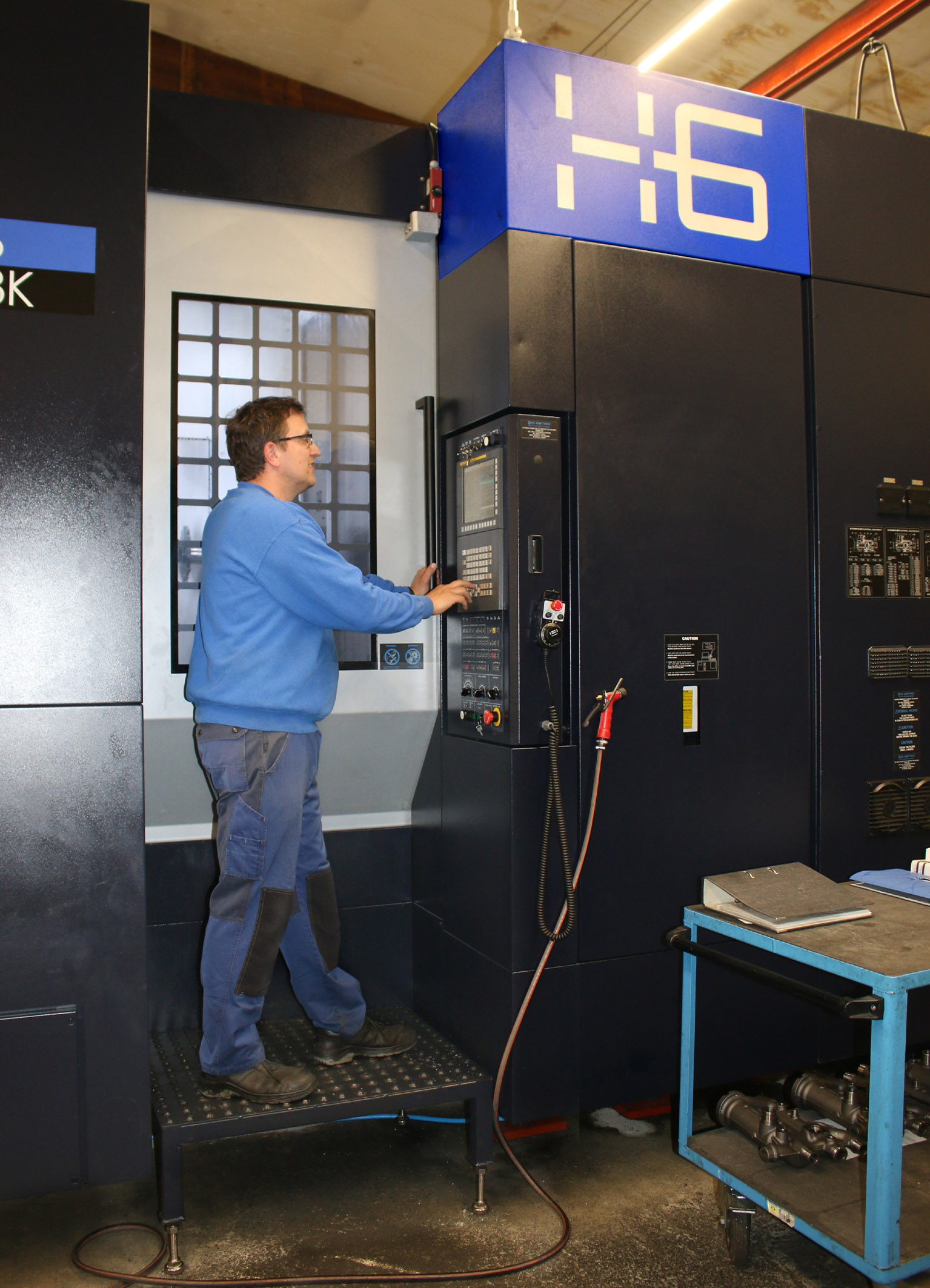
Furthermore, four additional pallets were ordered as accessories, so that a total of six pallets are available for the machining center. All pallets are equipped with a media passage for hydraulic clamping and a pneumatic system monitoring installation. Since Johne has its own fixture construction, these can already be equipped in an expanded state and prepared for one of the subsequent orders.
Good Price-Performance Ratio
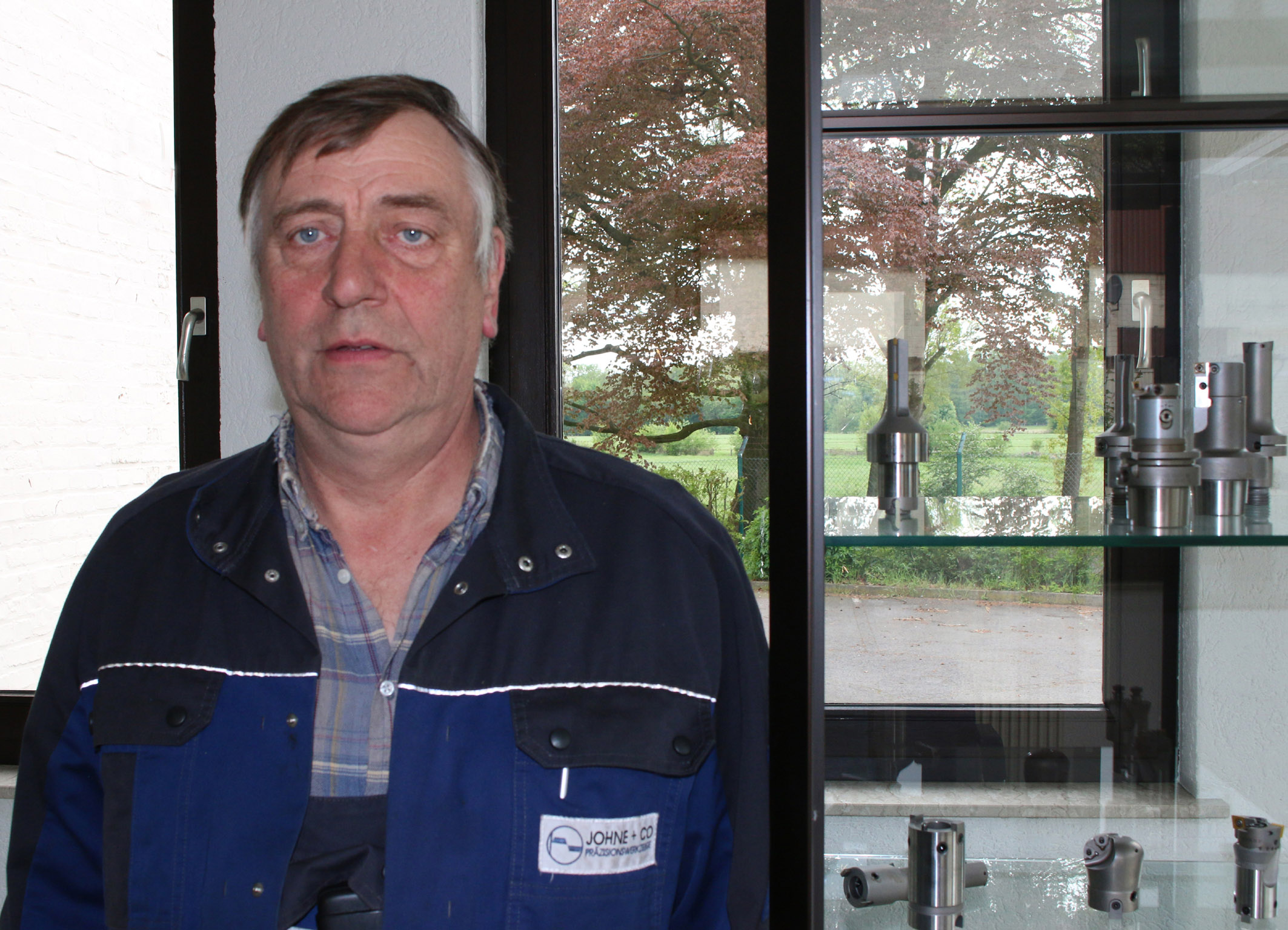
The HWACHEON H6 was delivered and installed in February of this year and has proven itself in the tough three-shift operations of the subcontractor. Ludger Krampe is satisfied with the machine: “Besides the high precision, it convinced us most notably with its good price-performance ratio, the numerous equipment options, and the extensive accessories.”
Johne Corporate Group
The Johne & Co. corporate group consists of two companies: Johne & Co. Präzisionswerkzeuge GmbH, based in Dorsten, and A+K Präzision GmbH in Haan, each with 70 employees.
Johne & Co. Präzisionswerkzeuge GmbH was founded in 1993 when four former employees took over the then-insolvent Kühn GmbH and continued the business operations under a new name. In 1997, A+K Präzision in Haan was added.
More information about the Johne group: www.johne-co.de