Over 80 years of detailed experience: Hwacheon combines traditional craftsmanship with modern technology. Our expertise in machine tool manufacturing ensures high production quality and continuous innovation for future-proof concepts in the German market.
VT-1650
Category
Large Vertical Turning LathesAvailable with
- Siemens 828D
- Harmony
- Fanuc 31i
- Fanuc 0i Plus
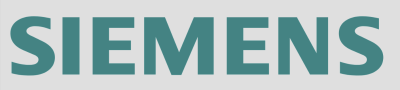
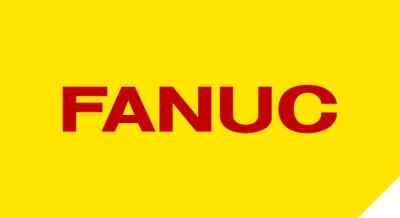
Size of VT-1650
- Max. cutting diameter2000mm
- Chuck-Size1651mm
- Swing over bed2100mm
Tradition Meets Modernity
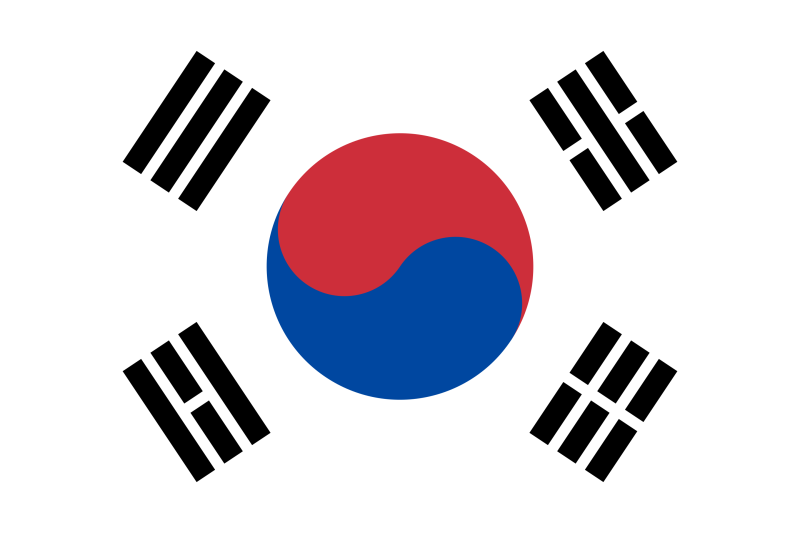
Flat Guides
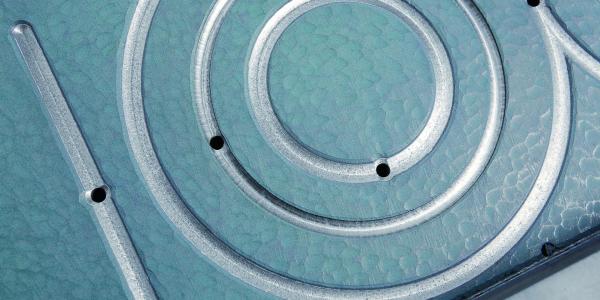
Excellent Damping Properties: Box or flat guides effectively absorb vibrations from the machining process by transferring them into the machine bed due to their large contact surface. Hand-fitted and scraped by experienced staff, these guides ensure precision. Central oil lubrication provides continuous lubrication with bedway oil, while the Turcite coating on the sliding surface offers excellent emergency running properties. Machines with flat guides are more durable and can handle higher chip volumes. Thanks to these unique features, they are considered particularly powerful and reliable.
Why choose us?
Satisfaction Guaranteed
Partnership that counts: Long-term customer relationships are characterized by transparency and continuous feedback. Our commitment to quality and service ensures an attractive price-performance ratio for our German customers.
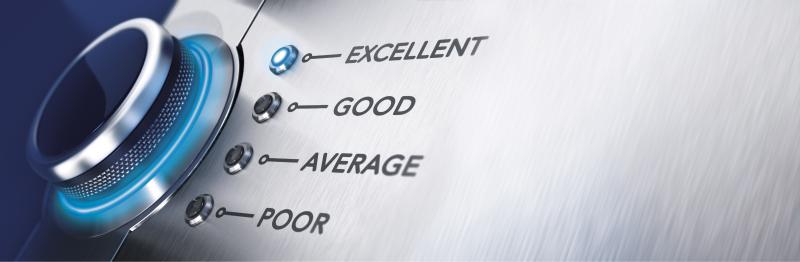
Tailor-Made
Flexibility is key: With extensive customization options, we design machines that exactly match your application. This gives you precise solutions for maximum efficiency and productivity in your business.
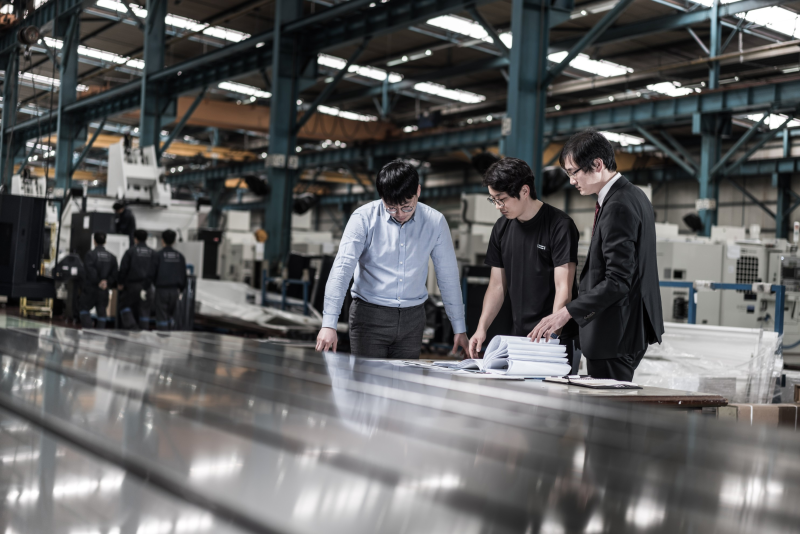
Performance in Focus
Power for your production: Our machines are designed for maximum productivity and availability. Top-class engineering and craftsmanship provide you with a crucial competitive advantage – all for your business success.
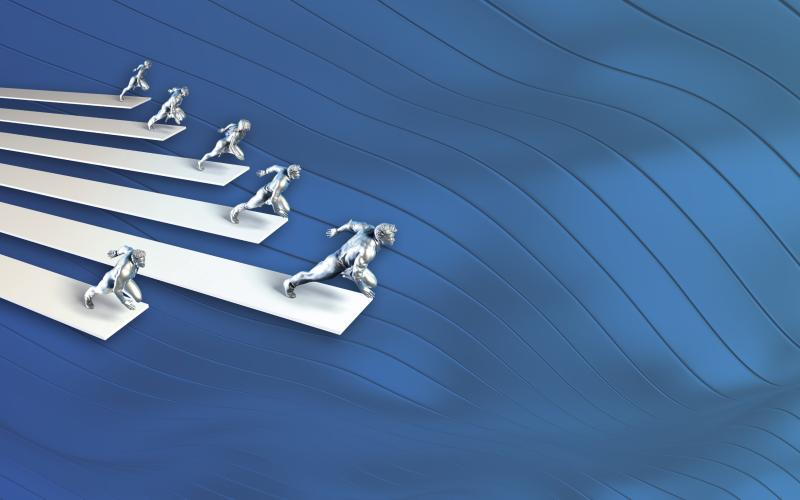
Technical Data
Item | Unit | VT-1650 |
---|---|---|
Table load | kg | 10000 |
Spindle power | kW | 45 |
Spindle speed | rpm | 250 |
Spindle torque | Nm | 27587 |
Machine weight | kg | 41400 |
NC-Control | Fanuc 0i TF Plus (Fanuc 31i-B Plus) | |
Floor space | m | 8,27 x 5,2 |
Max. cutting diameter | mm | 2000 |
Max. cutting length | mm | 1800 |
Chuck-Size | mm | 1651 |
Swing over bed | mm | 2100 |
Driven tools, max. Power | kW | 26 |
Torque of driven tools | Nm | 386 |
Axis-Stroke (X / Z / W) | mm | 1810 / 1000 / 800 |
Features of VT-1650
Flat Guides
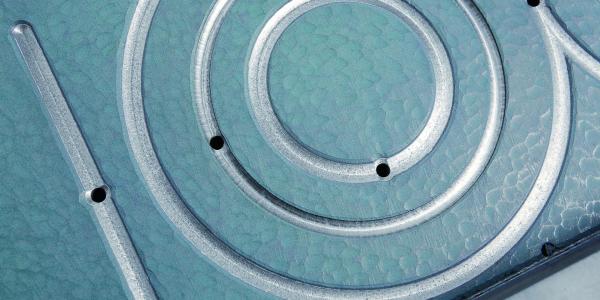
Excellent Damping Properties: Box or flat guides effectively absorb vibrations from the machining process by transferring them into the machine bed due to their large contact surface. Hand-fitted and scraped by experienced staff, these guides ensure precision. Central oil lubrication provides continuous lubrication with bedway oil, while the Turcite coating on the sliding surface offers excellent emergency running properties. Machines with flat guides are more durable and can handle higher chip volumes. Thanks to these unique features, they are considered particularly powerful and reliable.
Powerful Gear Spindle
High-Torque Drives for Heavy Machining: Lathes with gear spindles offer significantly higher torque than those with motor spindles. By selecting the appropriate gear ratio, torque can be optimally utilized within the speed range of the ideal cutting speed. Large spindle bearings and shaft diameters robustly absorb process forces and peaks, ensuring high durability. The gear stage can be conveniently selected via M-functions.
- Spindle power45kW
- Spindle speed250rpm
- Spindle torque27587Nm
Motor Spindle
Dynamics and Accuracy Perfectly Combined: Integrated motor spindles provide excellent acceleration and deceleration behavior as well as high holding forces. Thanks to an efficient cooling system, thermal growth and influence are minimized. This is particularly beneficial for turning-milling operations with high demands on dynamics and precision.
- Spindle power45kW
- Spindle speed250rpm
- Spindle torque27587Nm
Milling Spindle
Versatility and Precision with the Hwacheon Milling Spindle!: Discover the exceptional capabilities of the Hwacheon milling spindle with B-axis, transforming your lathe into a versatile five-axis solution. Enjoy perfect freeform surfaces thanks to simultaneous 5-axis interpolation on both the main and counter spindles. Benefit from seamless integration with your CAD/CAM systems for precise programming and experience a continuous process with our advanced look-ahead function. Thanks to thermal compensation, you achieve high surface quality and flawless transitions—all combined in Hwacheon’s in-house manufacturing excellence.
- Driven tools, max. Power26kW
- Torque of driven tools386Nm
RAM Spindle
Maximum Machining Freedom and Efficiency with the Innovative RAM Spindle!: Our state-of-the-art RAM spindle revolutionizes your machining with automatic tool change (ATC). This enables internal turning to great depths and allows for internal and angled bores. With the RAM spindle, you expand your machining options and significantly boost your efficiency.
- Driven tools, max. Power26kW
Driven Tools
Precision and Versatility Combined: Driven tools on lathes significantly expand machining capabilities. They enable milling, drilling, and other processes directly on the lathe, reducing re-clamping operations and minimizing downtime. Using various tools in a single setup increases machining accuracy and boosts overall productivity.
- Driven tools, max. Power26kW
- Torque of driven tools386Nm
Internal Coolant Supply
ICS Makes the Difference!: The internal coolant supply (ICS) delivers coolant directly to the cutting edge, optimizing lubrication and chip removal. It boosts productivity, extends tool life, and enhances process reliability.
Excellent Chip Disposal
Perfect Chip Removal for Your Machine!: Our innovative chip disposal systems reliably remove chips, reduce heat, and optimize machining. High-quality components ensure uninterrupted operation and maximum process reliability.