Over 80 years of detailed experience: Hwacheon combines traditional craftsmanship with modern technology. Our expertise in machine tool manufacturing ensures high production quality and continuous innovation for future-proof concepts in the German market.
i2
Category
Multitasking LathesMachine series
i - SeriesAvailable with
- Sinumerik One
- Fanuc 31i
- Fanuc 0i Plus
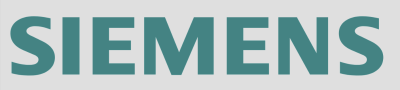
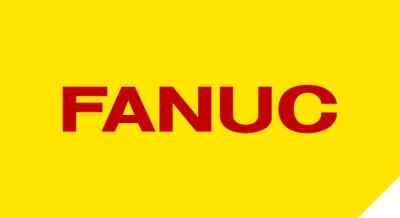
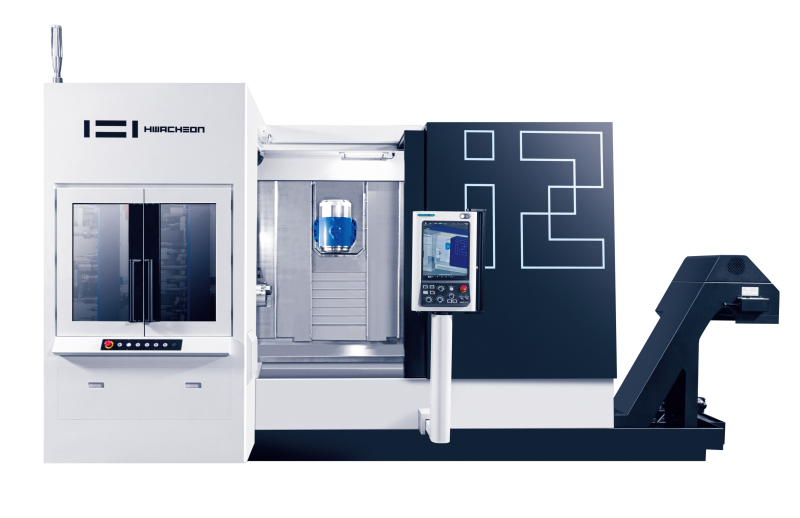
Size of i2
Max. cutting diameter | mm | 600 |
Chuck-Size | mm | 200 |
Swing over bed | mm | 600 |
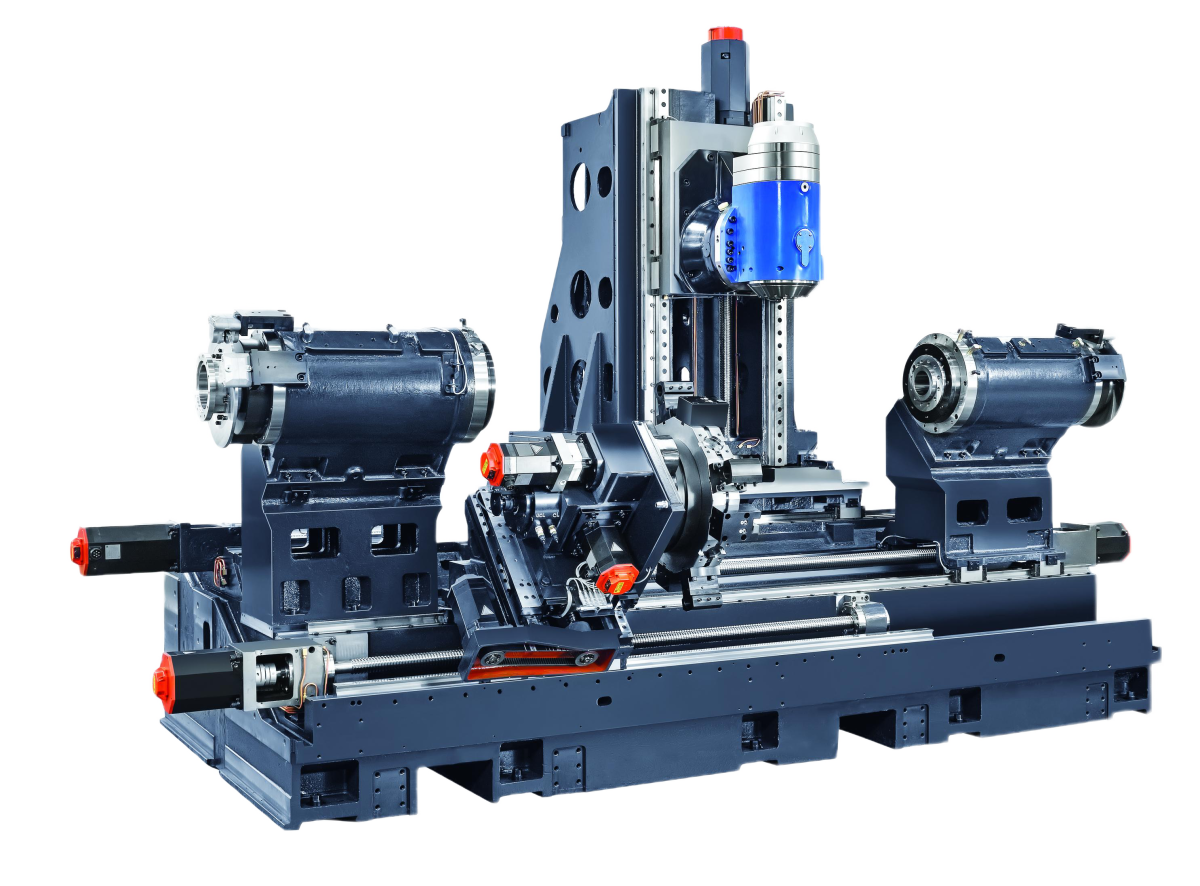
Tradition Meets Modernity
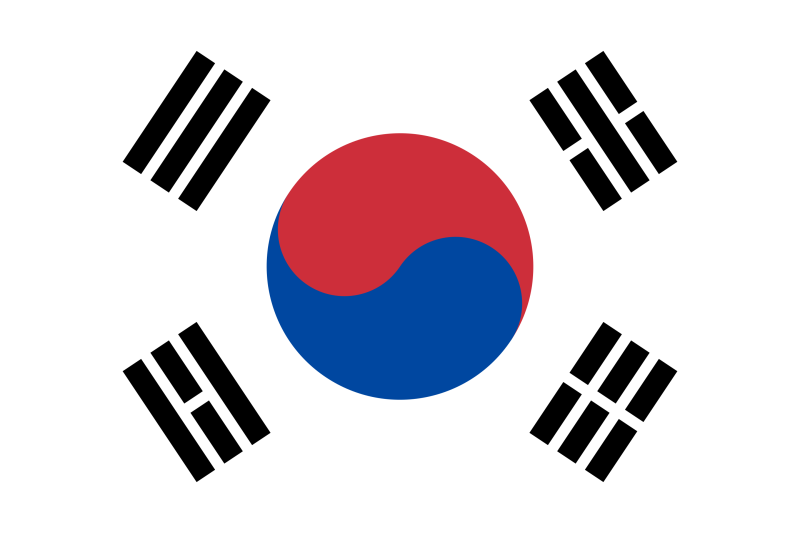
Dynamic Linear Guides
Speed and Dynamics Combined: Linear roller guides provide high dynamics and rapid traverse speeds. The workpiece weight is transferred linearly to the rollers, which must withstand enormous pressure at contact points. Therefore, we exclusively use linear roller guides from renowned manufacturers.
Why choose us?
Future-Proof Solutions
Innovation in every machine: State-of-the-art technologies shape our machine concepts, based on the latest standards for turning and milling machines. You benefit from efficient solutions, customized to your requirements.
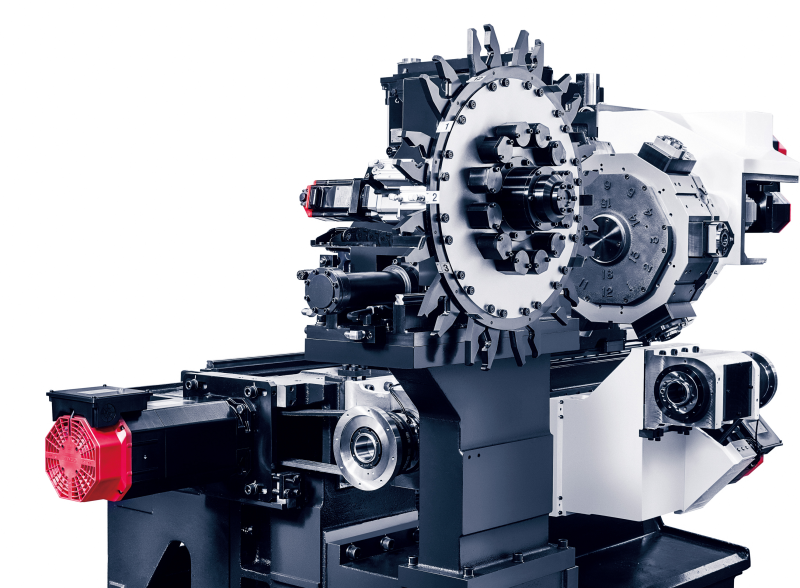
Tradition Meets Modernity
Over 80 years of detailed experience: Hwacheon combines traditional craftsmanship with modern technology. Our expertise in machine tool manufacturing ensures high production quality and continuous innovation for future-proof concepts in the German market.
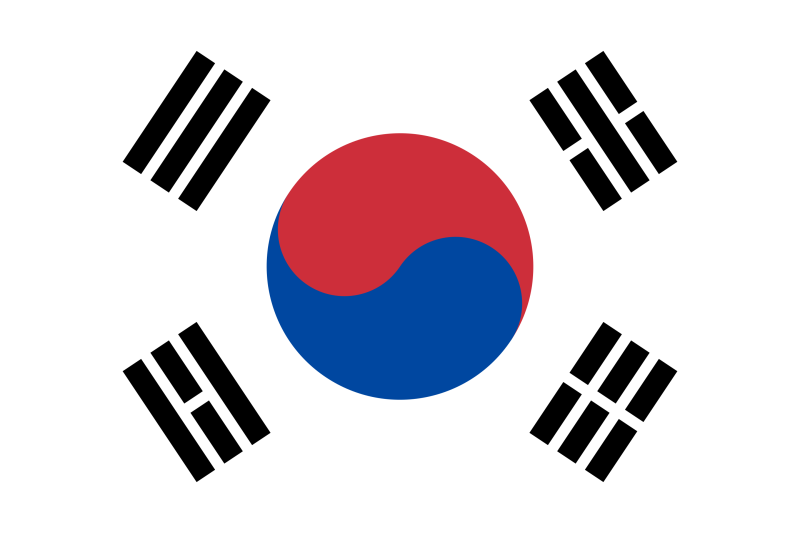
In-House Quality
Quality is created here: With our own manufacturing depth, including foundry and spindle production, we ensure durable and reliable machines. Quality and control go hand in hand to meet the German standards.
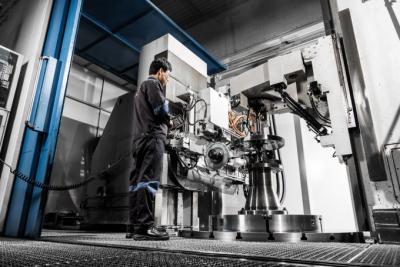
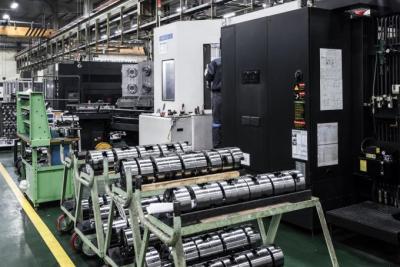
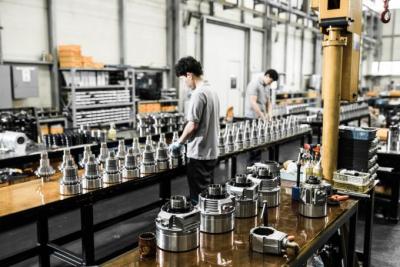

Technical Data
Item | Unit | i2 |
---|---|---|
Axis-Stroke (X / Y / Z) | mm | 630 / 300 / 1160 |
Spindle power | kW | 22 / 15 |
Spindle speed | rpm | 5000 |
Spindle torque | Nm | 467 |
Number of tools | Amount | 40 (80) |
Machine weight | kg | 14000 |
NC-Control | Fanuc 0i + Harmony | |
Max. cutting diameter | mm | 600 |
Max. cutting length | mm | 1100 |
Chuck-Size | mm | 200 |
Swing over bed | mm | 600 |
Max. Bar size | mm | 76 |
Driven tools, max. Power | kW | 22 |
Coolant tank vol. | Liter | 310 |
Features of i2
Motor Spindle
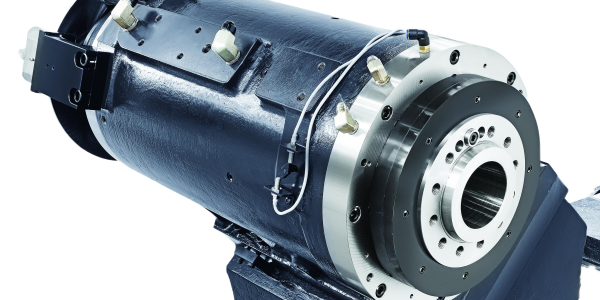
Dynamics and Accuracy Perfectly Combined: Integrated motor spindles provide excellent acceleration and deceleration behavior as well as high holding forces. Thanks to an efficient cooling system, thermal growth and influence are minimized. This is particularly beneficial for turning-milling operations with high demands on dynamics and precision.
Spindle power | kW | 22 / 15 |
Spindle speed | rpm | 5000 |
Spindle torque | Nm | 467 |
Max. Bar size | mm | 76 |
Counter Spindle
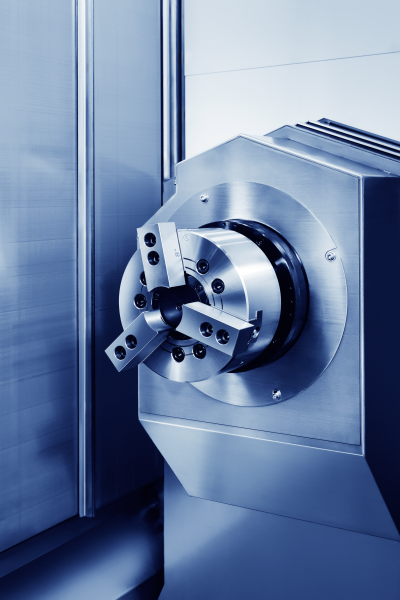
Precision in Every Dimension: Lathes with a counter spindle enable back-side machining of workpieces and can alternatively be used as an NC tailstock. This back-side machining saves time and effort by eliminating the need for re-clamping on another machine. It also improves precision since the workpiece does not need realignment. For enhanced process stability and safe ejection of finished workpieces, optional pneumatic or mechanical ejectors and spindle flushing can be added.
Turning-Milling Center
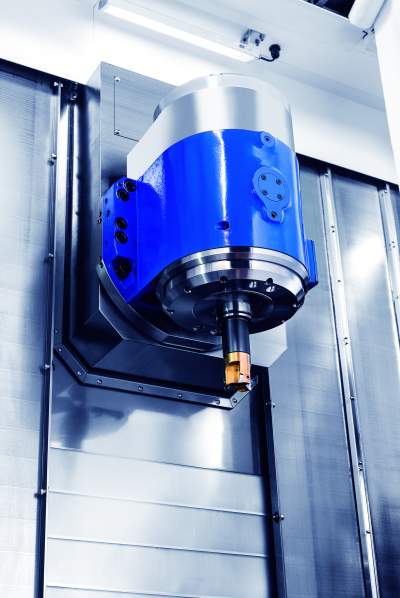
Complex Machining, Precise Contours: Turning-milling centers equipped with B-axes enable the creation of angled bores, milling of arbitrary contours, and demanding internal machining and gearing operations. These machines are ideal for processing complex geometries, offering high flexibility and precision in manufacturing sophisticated workpieces.
Driven tools, max. Power | kW | 22 |
Milling Spindle
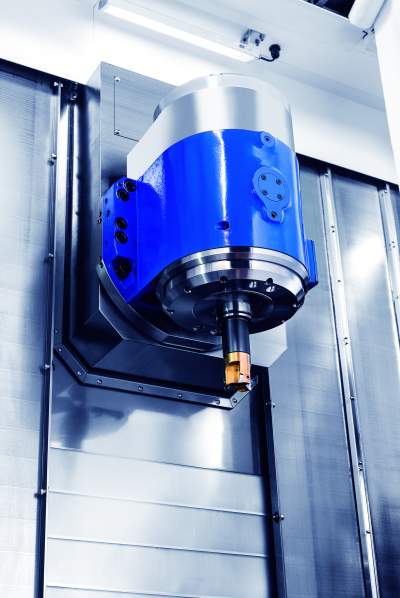
Versatility and Precision with the Hwacheon Milling Spindle!: Discover the exceptional capabilities of the Hwacheon milling spindle with B-axis, transforming your lathe into a versatile five-axis solution. Enjoy perfect freeform surfaces thanks to simultaneous 5-axis interpolation on both the main and counter spindles. Benefit from seamless integration with your CAD/CAM systems for precise programming and experience a continuous process with our advanced look-ahead function. Thanks to thermal compensation, you achieve high surface quality and flawless transitions—all combined in Hwacheon’s in-house manufacturing excellence.
Driven tools, max. Power | kW | 22 |
Clamping Technology
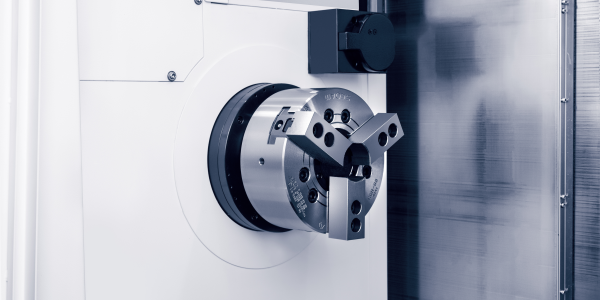
Chuck-Size | mm | 200 |
Automatic Tool Changer
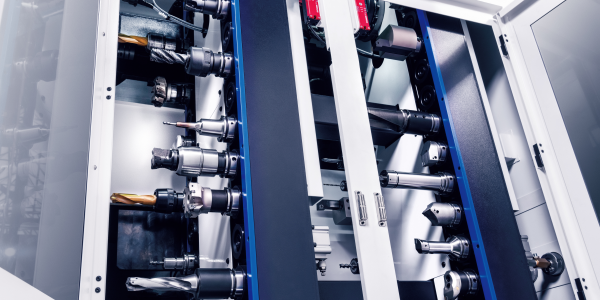
Number of tools | Amount | 40 (80) |
Excellent Chip Disposal
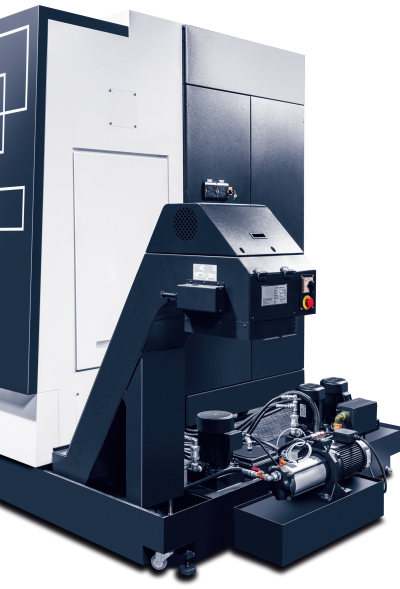
Perfect Chip Removal for Your Machine!: Our innovative chip disposal systems reliably remove chips, reduce heat, and optimize machining. High-quality components ensure uninterrupted operation and maximum process reliability.
Coolant tank vol. | Liter | 310 |
Workspace
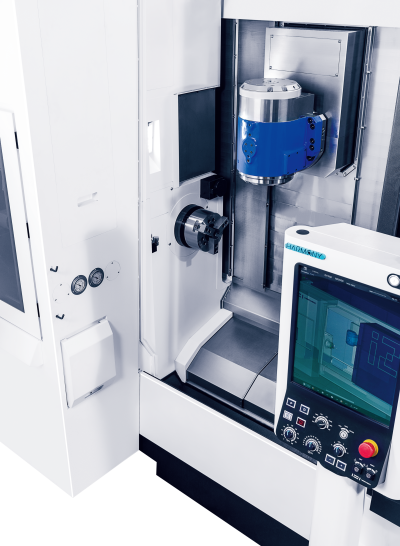
Peripherals and accessories
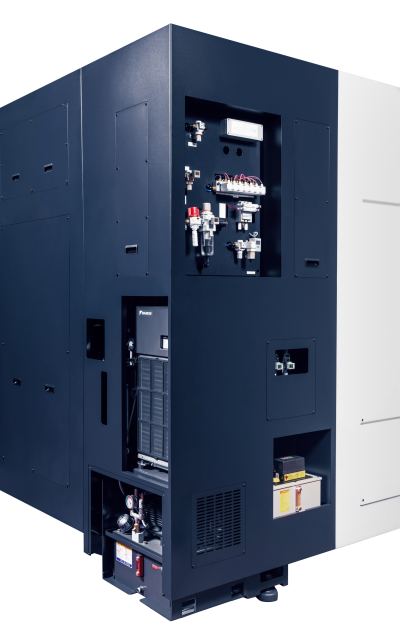
Y-Axis
Greater Flexibility and Time Savings: Lathes with a Y-axis enable 3-axis interpolation movements and the creation of off-center bores and milling operations. This allows workpieces to be fully machined in a single setup, eliminating operations on other machines and increasing machining accuracy. Additionally, they optimize grooving and parting processes by reducing lever forces for faster workflows.
- Axis-Stroke (X / Y / Z)630 / 300 / 1160mm
Driven Tools
Precision and Versatility Combined: Driven tools on lathes significantly expand machining capabilities. They enable milling, drilling, and other processes directly on the lathe, reducing re-clamping operations and minimizing downtime. Using various tools in a single setup increases machining accuracy and boosts overall productivity.
- Driven tools, max. Power22kW
Twin Turret Technology
Maximum Productivity, Minimum Machining Time: Twin-turret lathes, also known as double-turret lathes, offer significant advantages in reducing machining time. Simultaneous tool deployment enables roughing and finishing on one side while the main and counter spindles operate independently. This design enhances efficiency and allows for complex machining strategies in less time.
High-Quality Spindle
Consistent Cooling and Lubrication for Maximum Precision: Our in-house manufactured spindles are cooled and lubricated by an innovative air-oil aerosol system, while temperature sensors ensure constant monitoring. This advanced technology guarantees exceptional durability and outstanding smoothness. Experience maximum precision with minimal thermal growth for consistent performance even under the most demanding conditions.
Dynamic Linear Guides
Speed and Dynamics Combined: Linear roller guides provide high dynamics and rapid traverse speeds. The workpiece weight is transferred linearly to the rollers, which must withstand enormous pressure at contact points. Therefore, we exclusively use linear roller guides from renowned manufacturers.
Internal Coolant Supply
ICS Makes the Difference!: The internal coolant supply (ICS) delivers coolant directly to the cutting edge, optimizing lubrication and chip removal. It boosts productivity, extends tool life, and enhances process reliability.
High-Quality Pretensioned Ball Screws
Thermal Stability for Precision and Reliability: Pretensioned ball screws reliably and stably compensate for thermal expansion. This technology prevents unwanted elongation of the spindles, ensuring lasting precision and consistently high machining accuracy over extended operating periods.
Effective Core Cooling of Ball Screws
Cool Efficiency for Longevity: The cooling system uses actively tempered oil that flows through a central bore in the ball screw. Precise temperature control reduces thermal expansion, increases accuracy, and minimizes wear, thereby extending the system’s lifespan.