Extreme Performance and Stability for Heavy Machining
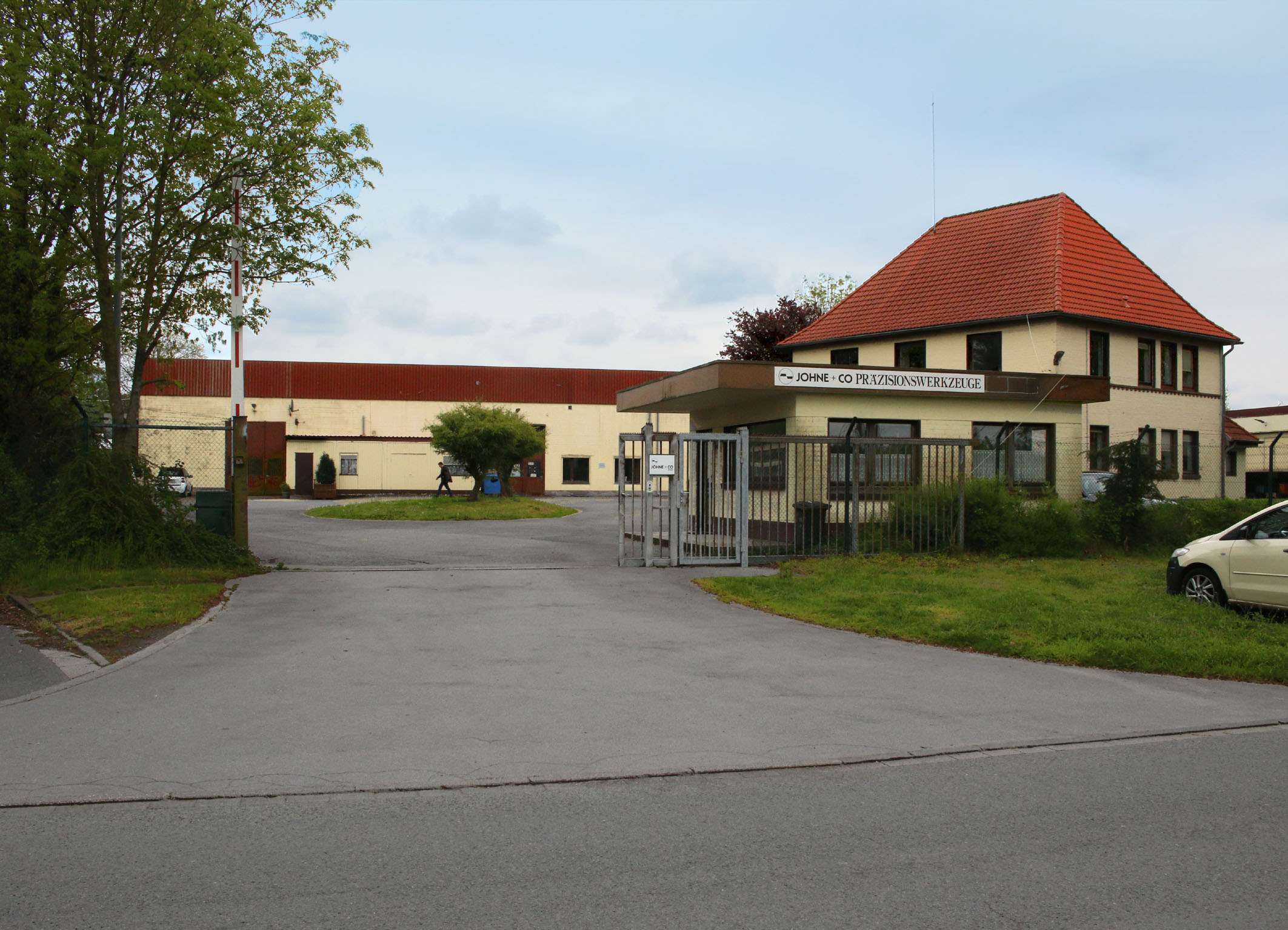
Contract manufacturing companies often work on a wide range of parts for their clients in various batch sizes, ranging from small series to mass production. The size and complexity of the workpieces also vary from order to order. Consequently, the machine tools used in this field must offer high flexibility with simultaneous high precision and repeatability. A contract manufacturer from southern Münsterland has recently started using a horizontal machining center with a pallet changer from the leading South Korean machine tool manufacturer HWACHEON for complete machining of workpieces with partially complex geometries.
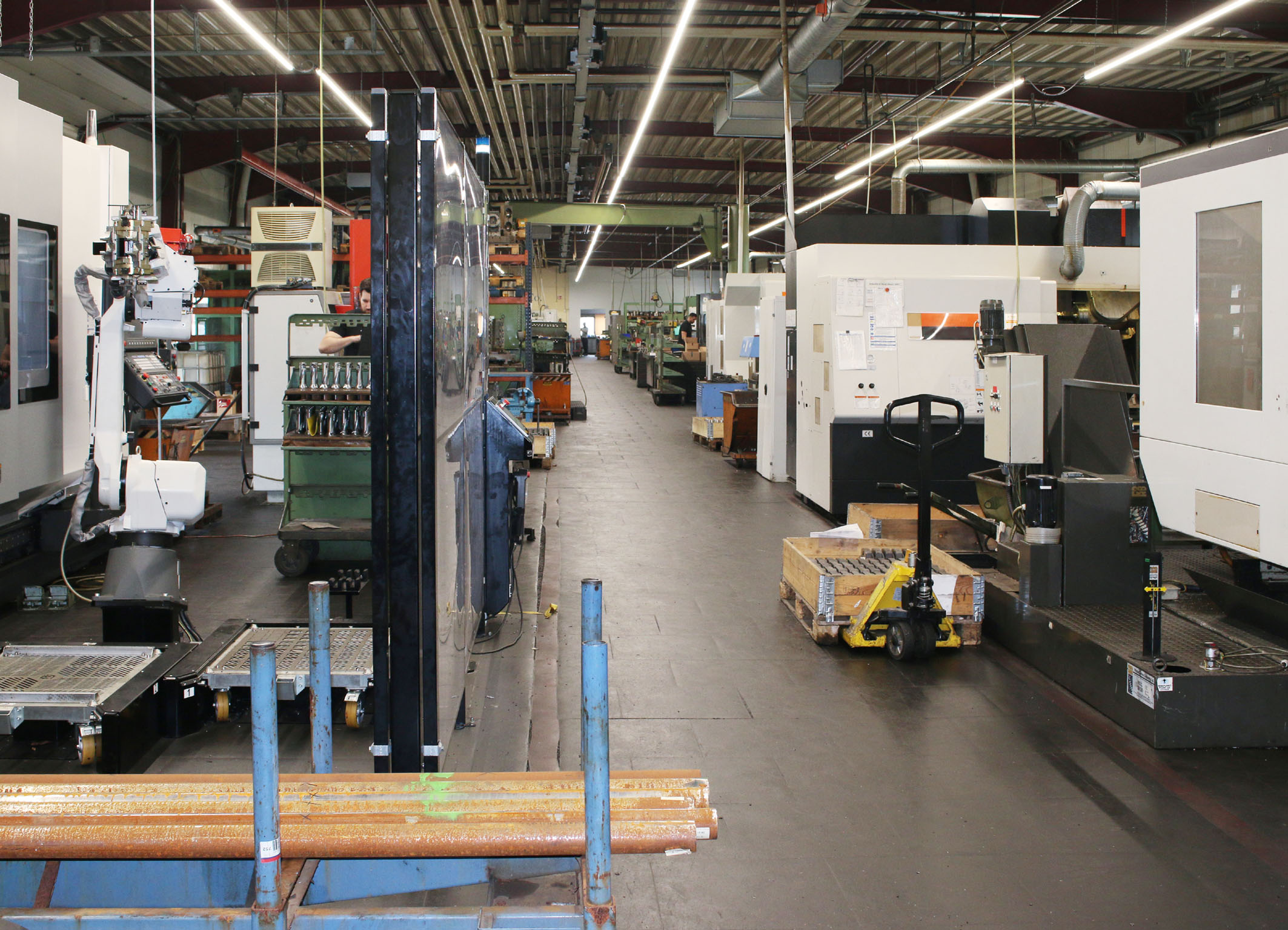
On the outskirts of the Dorsten district of Wulfen, the workshops of Johne & Co. Precision Tools GmbH are located in a picturesque setting overlooking wide meadows and fields. The company has two main areas in different product categories: Firstly, there is the production of precision tools for cutting technology, with a focus on boring and fine boring. In this segment, Johne holds over 16 patents and works with renowned companies in the carbide industry for development, who also assume the distribution of the products. Many boring and fine boring heads for cutting technology are "Made by Johne". A proprietary development here is the MicroCut tool line for fine boring applications, characterized by a patented fine adjustment.
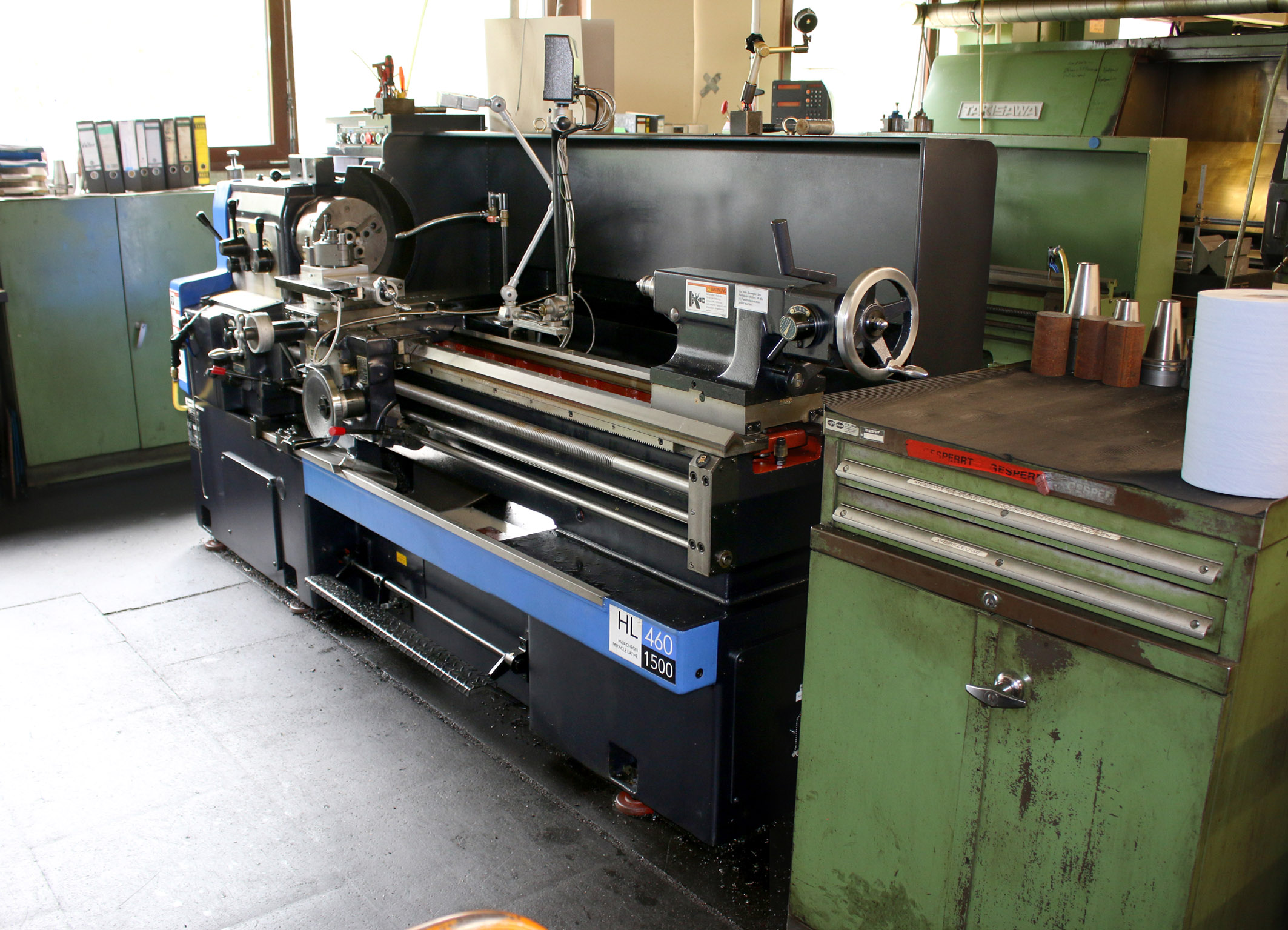
The company is very flexible regarding batch sizes: It offers the development and construction of prototypes starting from batch size 1. For precision tools, typically between one and 50 pieces are manufactured, and for special tools, the quantity is between one and three. However, the situation is different in the area of contract manufacturing: Here, batches start at 20 pieces and, for example, a batch for a special pump's component can reach a size of 20,000 per month.
High-Quality Machine Package
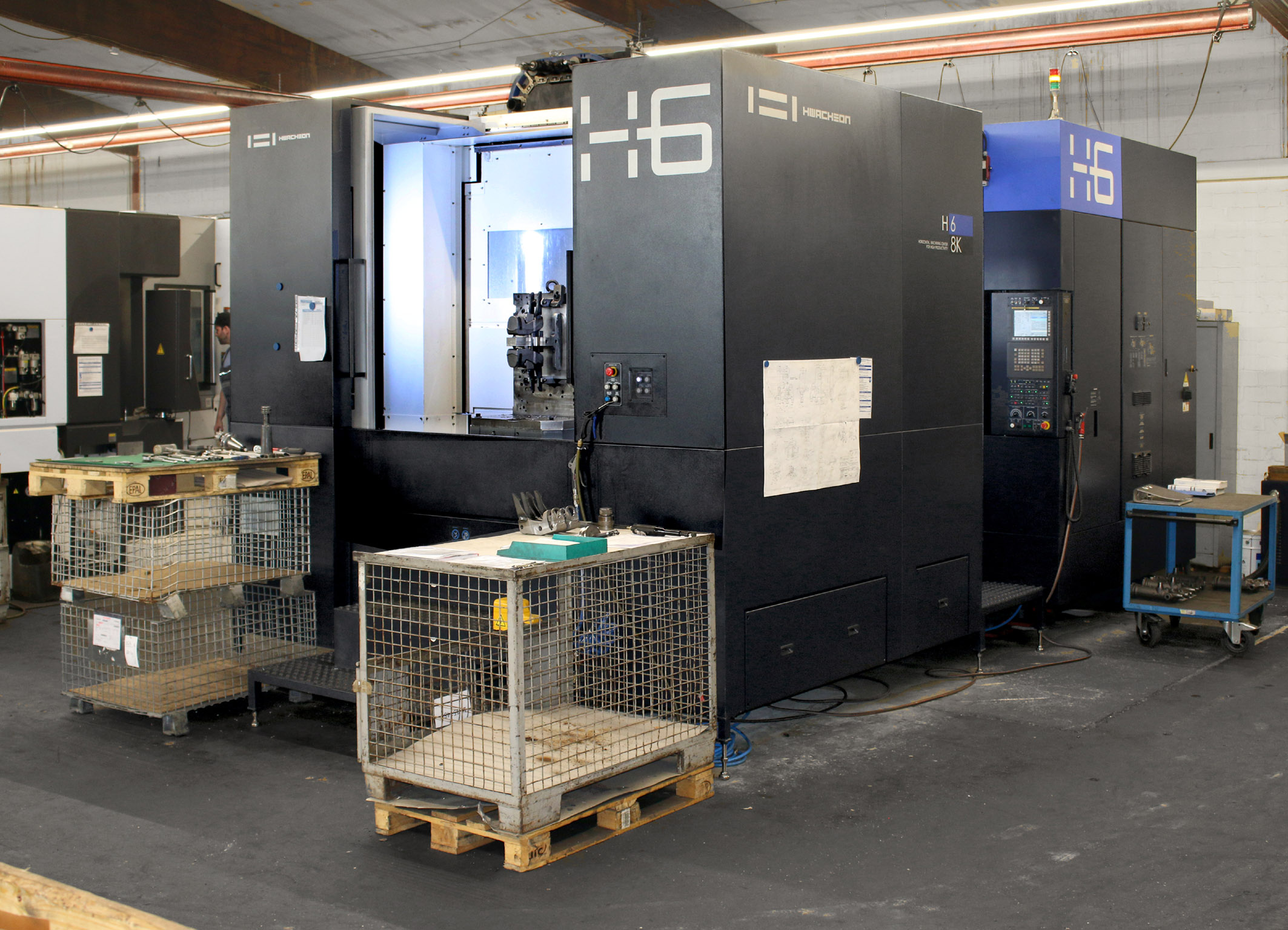
Continuous modernization of the machine park is also part of quality assurance at Johne. Additional machines are acquired as long as space in the two halls permits. In 2018, Ludger Krampe initially sought a conventional lathe. A formerly self-employed service technician drew his attention to the South Korean-made machine tools of his new employer. “I already knew the HWACHEON brand from the time when they were still distributed in Germany via Hommel, but I hadn't dealt with the machines themselves back then,” recalls Krampe. This quickly changed, as by the end of the decision-making process, a machine package was compiled, which included, alongside the conventional lathe, a horizontal machining center with extensive equipment. This process was accompanied by the HWACHEON European headquarters in Bochum, which provides customer service and fast spare parts supply.
Machining Center with a Wide Range of Applications
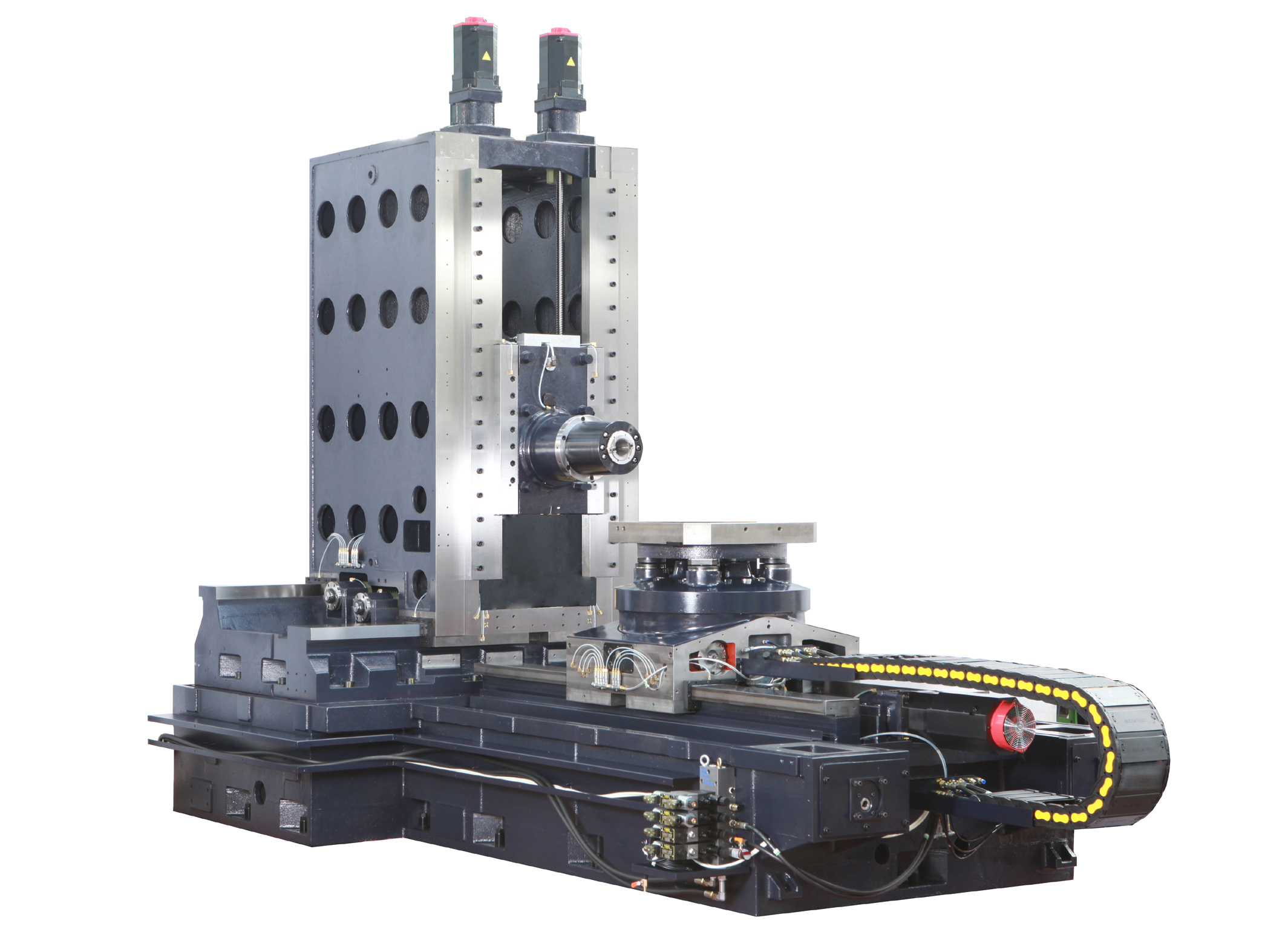
For heavy machining of workpieces with partially complex geometries, Ludger Krampe was looking for a suitable machining center and noticed the robust H-series from HWACHEON, which had just been introduced to the European market at that time. The envisaged horizontal machining center HWACHEON H6 is particularly stable and powerful in rough machining, while also enabling precise and dynamic finishing. Similar to its larger sister H8, it opens up a wide range of applications, from the series production of hard-to-machine precision parts to achieving high surface finishes in mold and tool making.
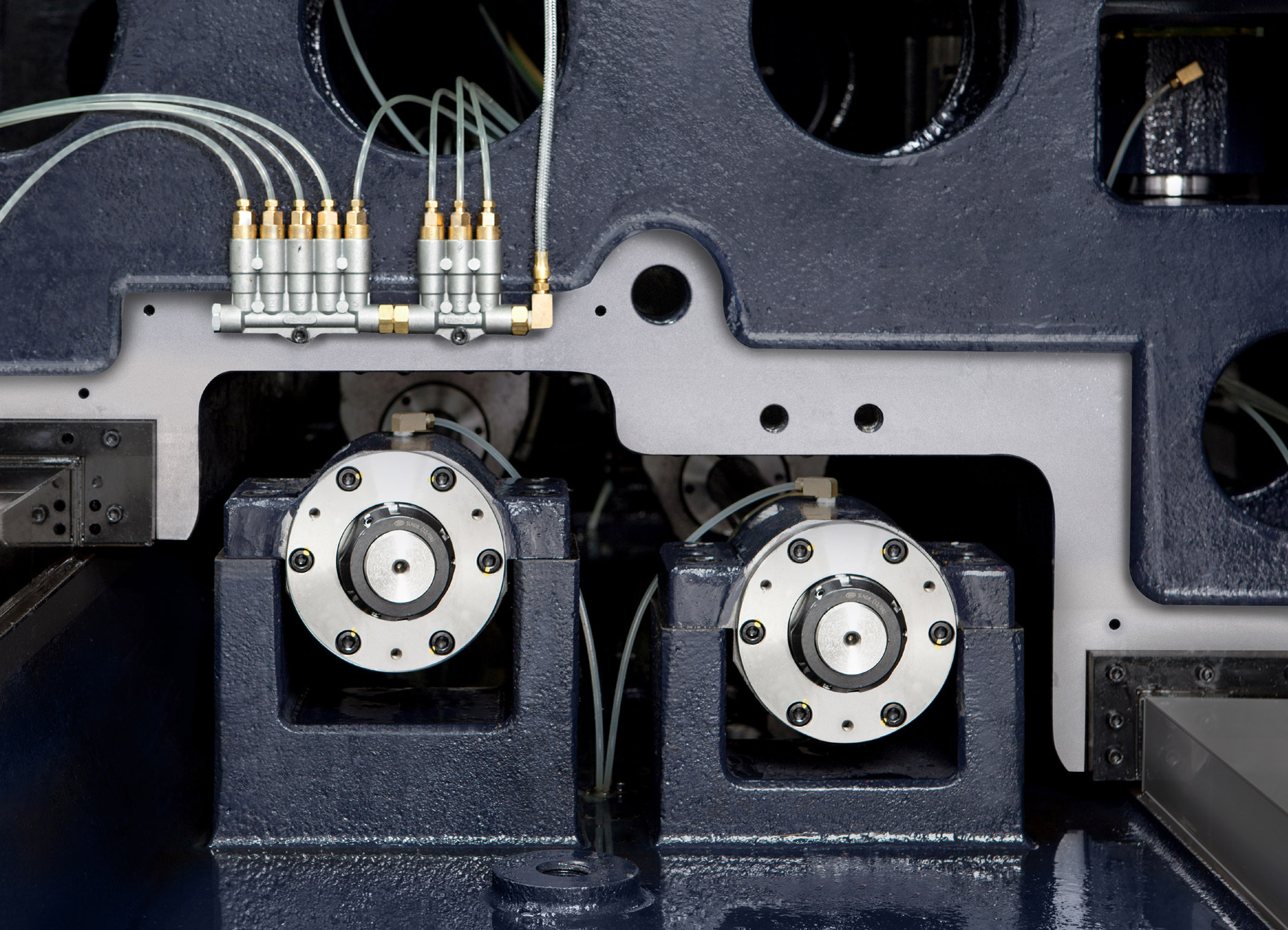
This is mainly achieved through the high weight of the H6 of 26.5 tons, and the massive and extremely rigid structure of both the machine bed and stand. The T-shaped bed is made of Meehanite casting and is thermosymmetrically built, ensuring dimensional accuracy throughout the entire process, even during long and chip-intensive work sessions. The generously sized and hand-scraped flat guides, as well as the twin drives in the X and Y axes, enable precise and high cutting rates. Air-pressured flat guides lead to low breakaway torque and ensure smooth movements at rapid traverse speeds up to 48 m/min.
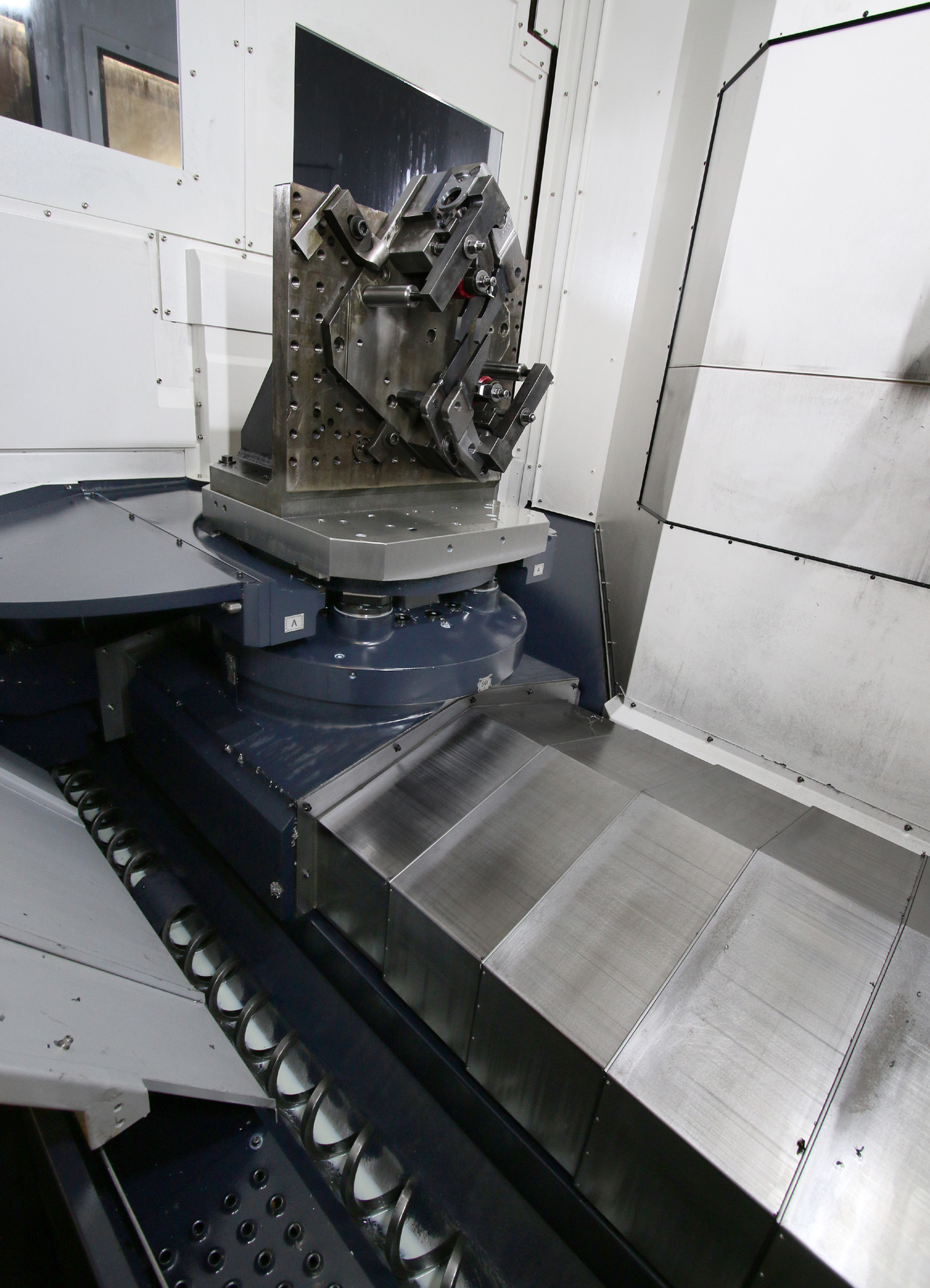
For economical series production, the H6 is equipped as standard with a pallet changer and two pallets measuring 630 x 630 mm. The backlash-free preloaded worm gear of the simultaneously controlled B-axis, combined with the directly controlling rotary encoder, ensures adherence to accuracy requirements.
Lots of Power and High Torque
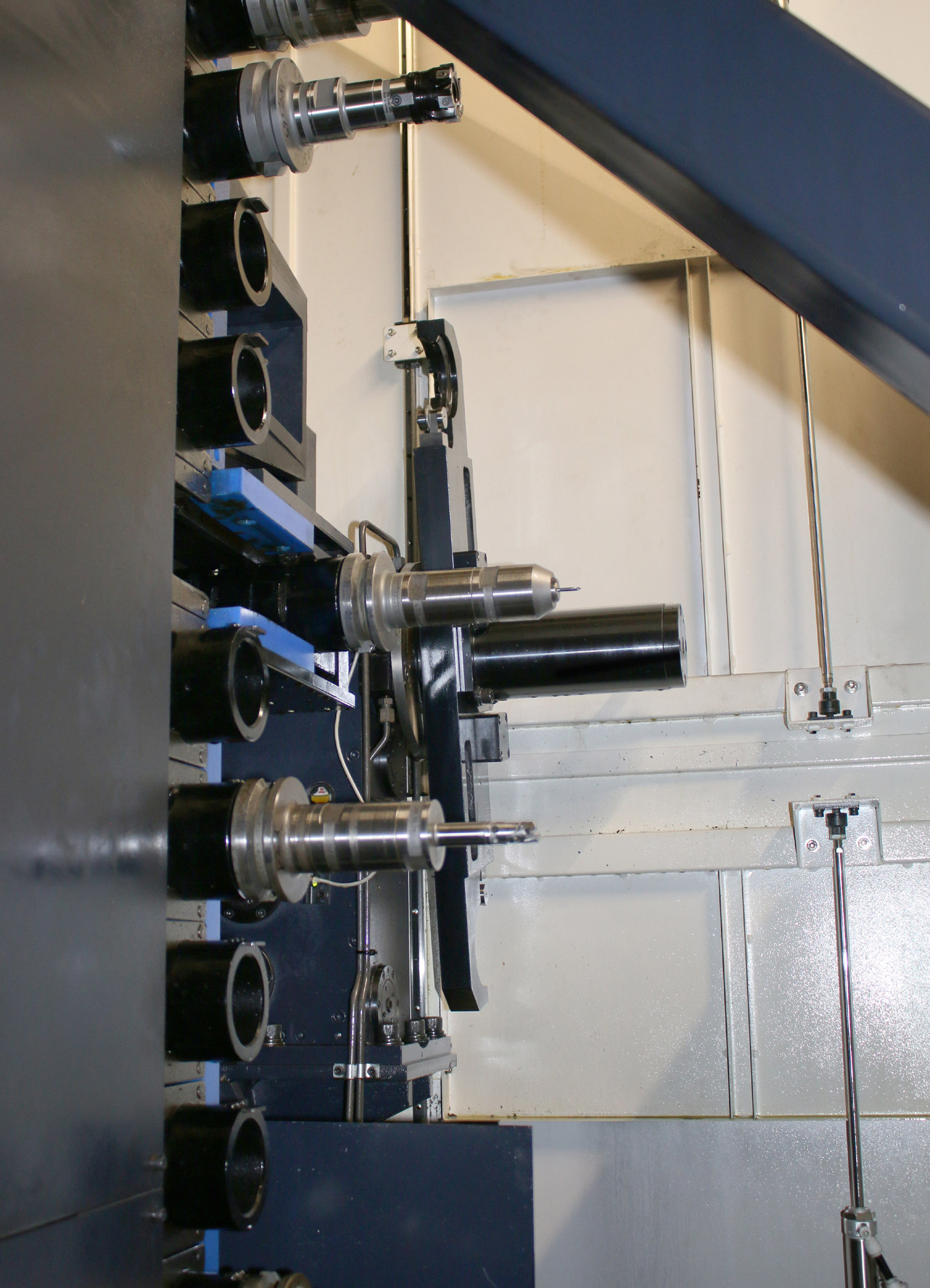
The Johne associate could choose between different options for equipping the machining center. It is available with either a Fanuc 31i or Siemens 840D control, with the decision made in favor of the Fanuc control. There were also two options for the spindle: a motor spindle with 12,000 rpm or a geared spindle. “Since we also machine super duplex steels on the machine, we needed a spindle with a lot of power and high torque,” says Ludger Krampe. “That's why we chose the geared spindle.” This spindle is manufactured by HWACHEON's own spindle production and is implemented as a two-stage model with outputs of 35 and 22 kW. At 8,000 rpm, it offers a torque of 1,654 Nm, thus easily fulfilling all requirements of heavy machining.
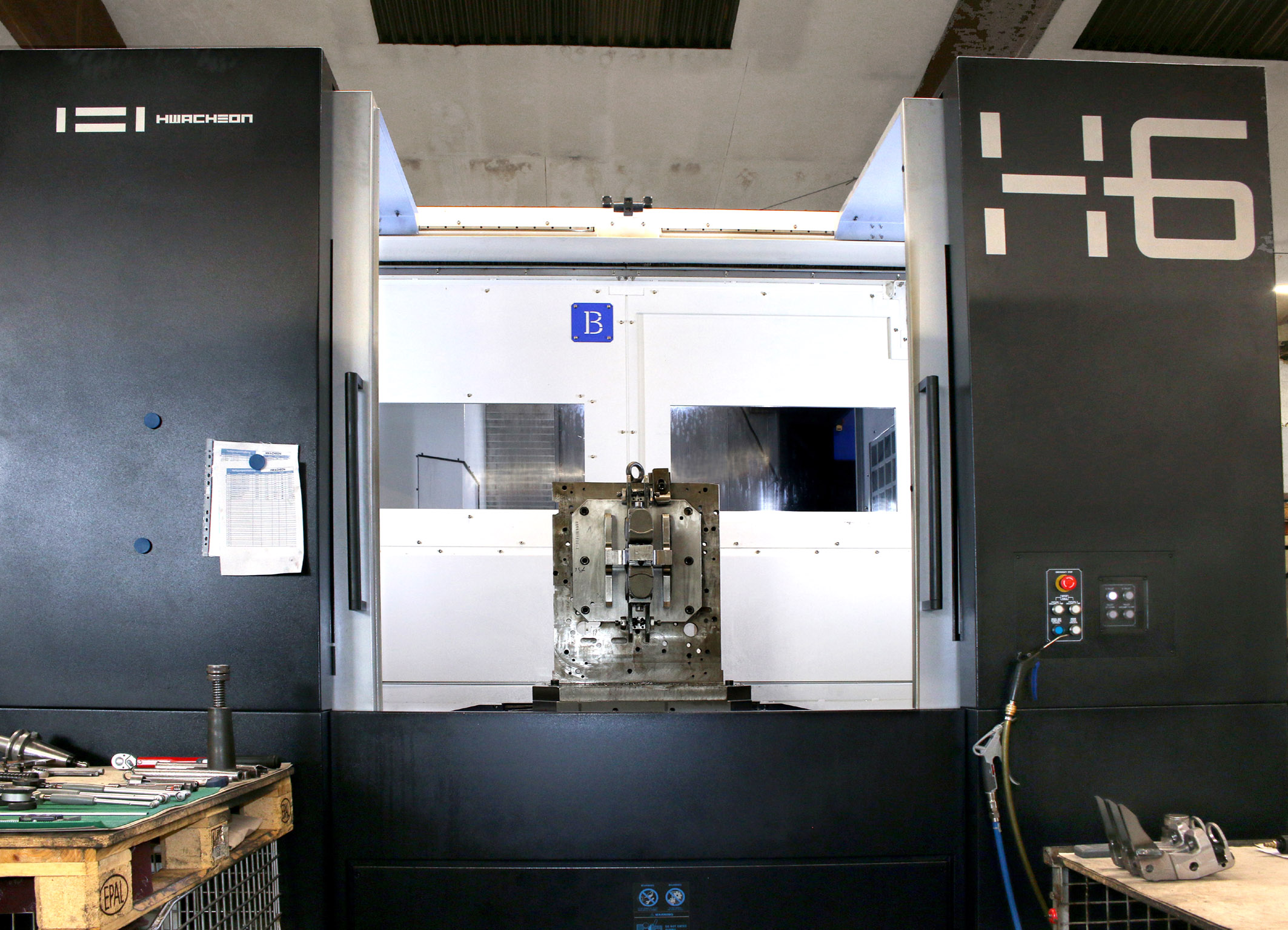
The tool magazine of the machine chosen by Johne offers 60 slots, providing what are actually sufficient capacities for machining complex workpieces with numerous tools. “But a few more slots could have been nice for us,” says Krampe with a smile. “After all, we need 20 to 25 tools to machine a workpiece.” These include roughing and finishing tools, drills of different diameters, thread cutters, and of course, the fine boring solutions from in-house production.
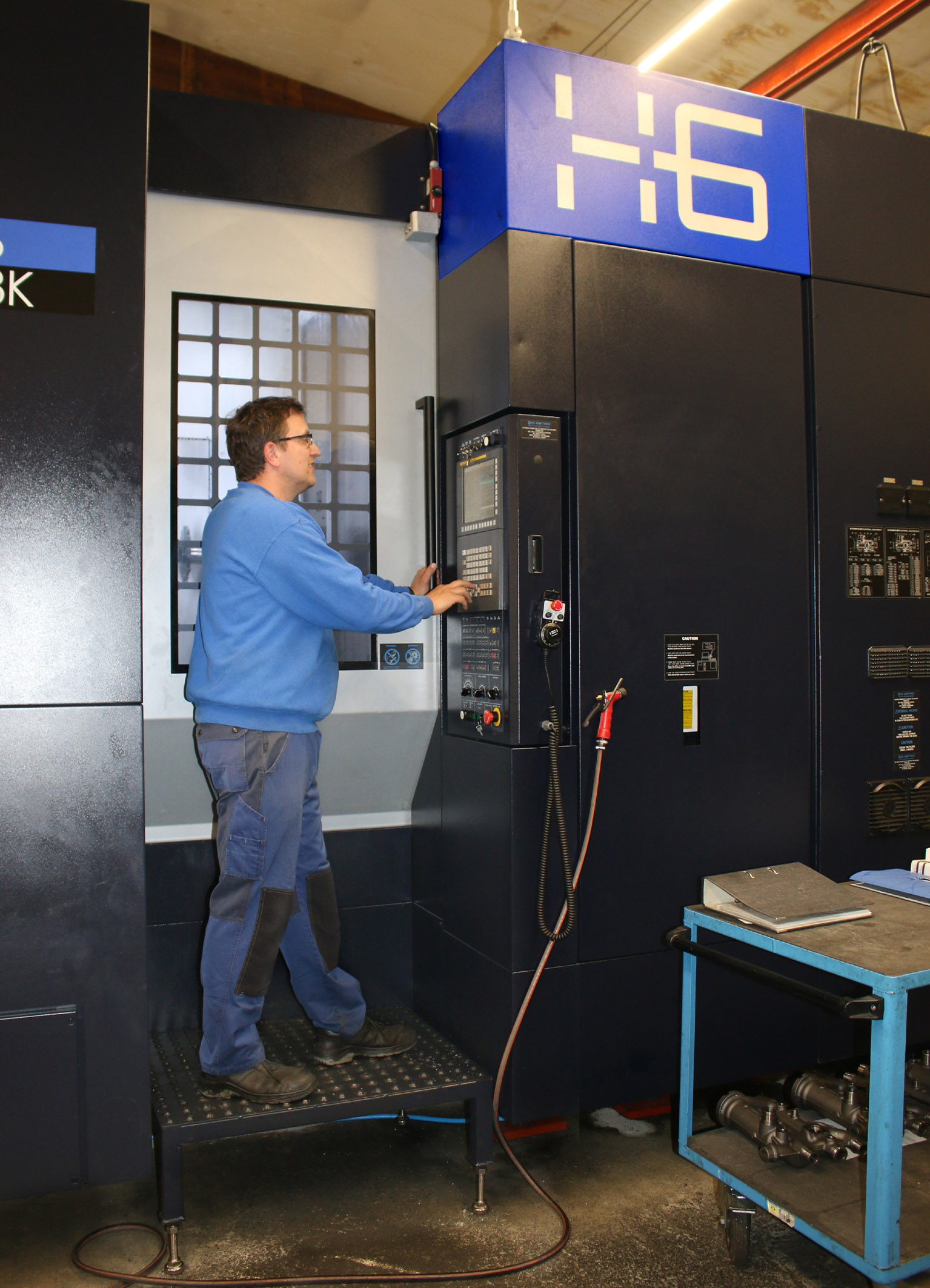
An additional four pallets were ordered as further accessories, so a total of six pallets are available for the machining center. All pallets are equipped with a media feedthrough for clamping hydraulics and a pneumatic system monitoring setup. Since Johne has its own fixture construction, these can already be equipped while they are disassembled and prepared for a subsequent order.
Good Price-Performance Ratio
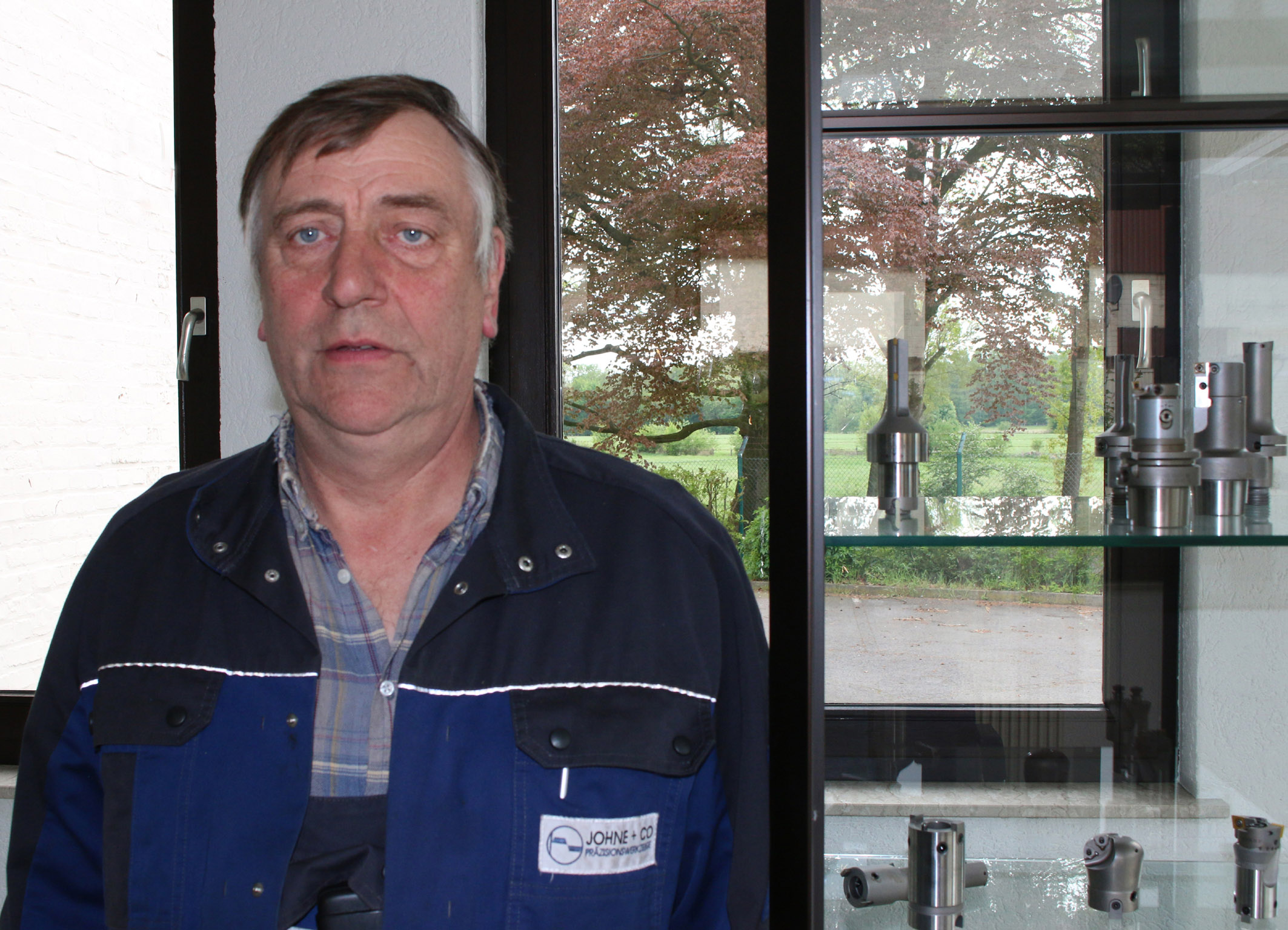
The HWACHEON H6 was delivered and set up in February of this year and has since proven itself in the demanding three-shift operation of the contract manufacturer. Ludger Krampe is satisfied with the machine: “In addition to the high precision, it has primarily convinced us with a good price-performance ratio, the numerous configuration options, and the extensive accessories.”
Johne Group
The Johne & Co. corporate group consists of the two companies Johne & Co. Precision Tools GmbH based in Dorsten and A+K Precision GmbH in Haan, each with 70 employees.
Johne & Co. Precision Tools GmbH was founded in 1993 when four former employees took over the then-insolvent Kühn GmbH and continued the business under a new name. In 1997, the Haan-based A+K Precision was added.
For more information about the Johne Group: www.johne-co.de