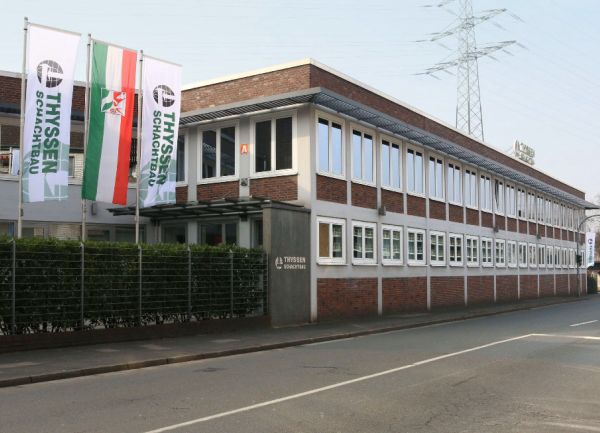
Even in the machining of large components, high precision is often crucial. Therefore, companies operating in this area must have a machine fleet that possesses the quality and stability required for high-performance machining. For example, TS Technology + Service GmbH in Mülheim an der Ruhr has decided to use a machining center from a South Korean machine tool manufacturer known for its powerful performance and robust construction for the milling of their smaller, large-volume workpieces weighing up to one ton. After six months of experience with the machine, the service company belonging to the THYSSEN SCHACHTBAU group takes stock:
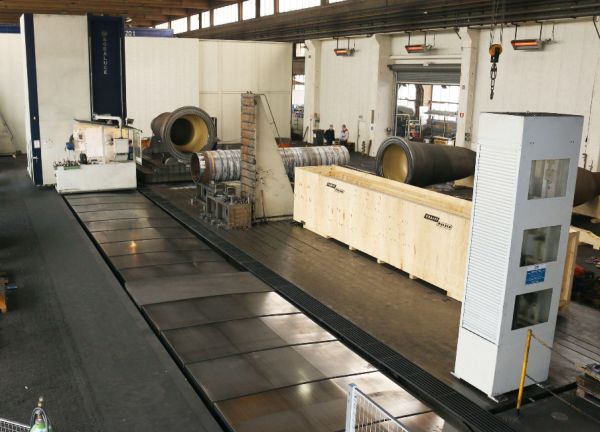
For many years now, the machining technology business unit of TS Technology + Service GmbH has been mechanically processing steel parts of all kinds with piece weights of up to 100 tons. In doing so, the company has developed into one of the leading specialists for high-performance machining of complex components and assemblies in large dimensions. To this end, the machine fleet has been continuously expanded and modernized to a high standard. In the past two years alone, three new machines have been purchased, including a heavy-duty lathe with a turning length of 10,000 mm. Particularly impressive is a large drilling plant that was put into operation in 2010, which is housed in its own hall section due to its dimensions. It offers a horizontal travel path of 24,000 mm and can accommodate large parts with up to 6,000 mm height and a weight of up to 100 tons. This meant a quantum leap in large-part machining for the Mülheim service provider.
Only about 15 percent of the orders come from the parent company THYSSEN SCHACHTBAU. Mainly, the independently operating large-mechanics specialist is now active for customers from power plant and smelting technology as well as various fields of mechanical engineering. For large-volume workpieces, small and very small batches, often with a batch size of one, dominate. “We also produce series of 120 to 140 pieces,” says Nebojsa Babic, department manager for machining technology, adding with a wink, “– but per year!”
Highly Qualified Employees
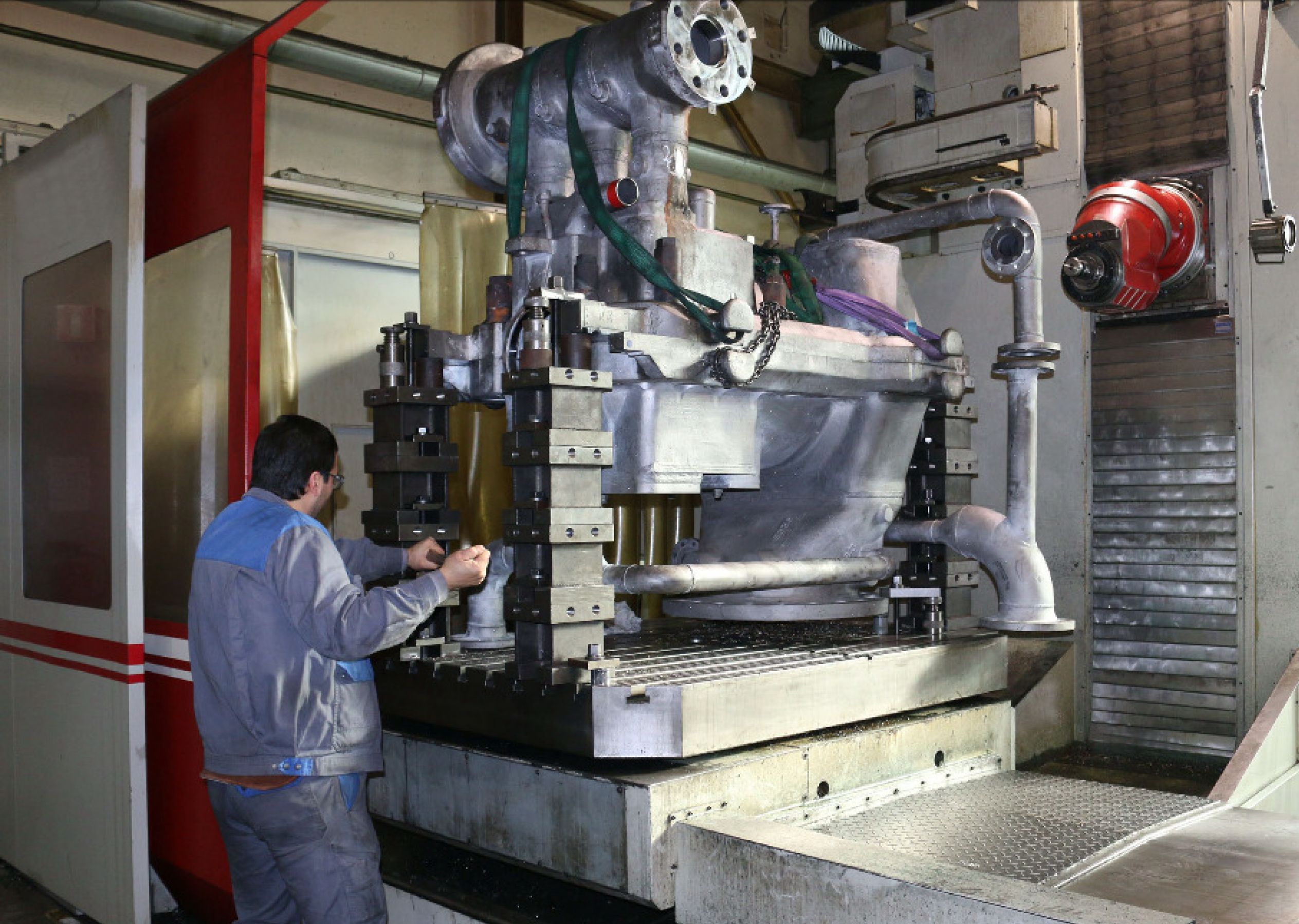
The machining of large parts with complex geometries is very demanding and requires a high degree of expertise. Even the smallest error would destroy the often several thousand euro expensive workpieces. Therefore, the company, certified according to DIN ISO 9001, invests heavily in the qualification and further training of the approximately 40 employees in the machining technology sector.
Extensive measuring and testing technology ensures control of the materials and the geometries of the machined parts. Aligning a two-part turbine housing on the machine table, for example, requires a lot of patience and a delicate touch. “Depending on the deflection of the two housing parts, this process can take eight to twelve hours,” explains Nebojsa Babic. As many as ten dial gauges are used in this process. After recording all relevant dimensions, the measurement protocol is presented to the client. After machining, the values achieved are also recorded and accepted by the customer, so that they can dispense with the usual goods receipt inspection, as the dimensional accuracy of the parts has already been proven by this service.
Milling Center for Smaller Large Parts
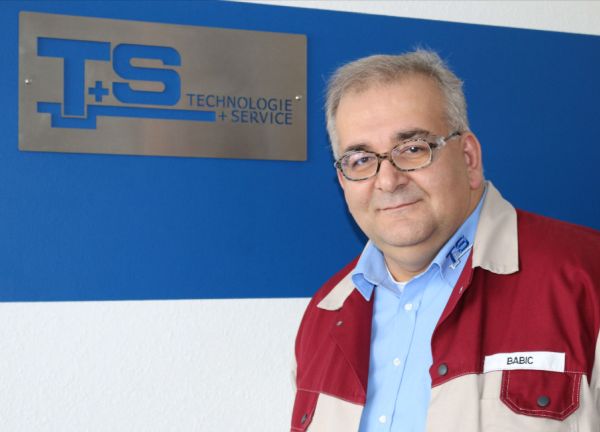
But not only the very large components are processed in Mülheim, piece weights of up to one ton are also part of the service spectrum. However, these parts are not processed on the large drilling machines, as this would be too costly and block urgently needed machine capacities. Rather, a separate milling machine is available for the smaller workpieces, which no longer met the increased quality requirements last year.
Therefore, the head of machining technology was looking for a powerful and robust milling center that also offers the highest precision. It should also be easy to operate, as trainees from the company are also integrated into production on this machine. Following a recommendation, he came across the vertical machining center for heavy machining VESTA-1050B from the South Korean machine tool manufacturer Hwacheon. He was able to view the machine in the technology center of the European headquarters in Bochum. “When I first saw what I thought was the small machining center, I had doubts due to its small size as to whether it would be the right one for us,” recalls Nebojsa Babic.
Designed for Heavy Machining

Objectively, however, the VESTA-1050B is not so small at all, with a length of 4,220 mm and a width of 3,090 mm. Thanks to the good accessibility of the work area, even large-volume workpieces can be easily clamped on the 1,150 x 600 mm machine table.
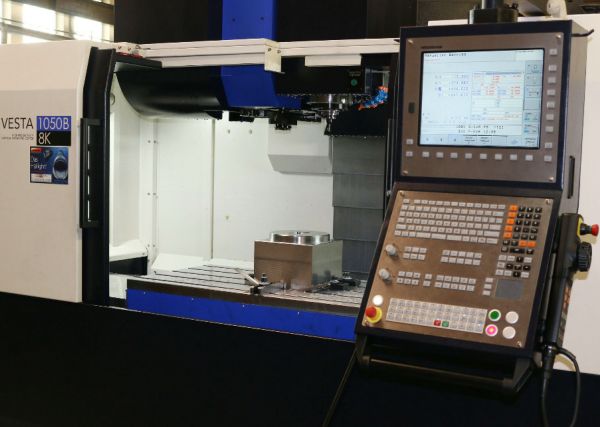
The machine is specifically designed by the manufacturer for heavy machining and offers tough, high-strength flat guides in all axes, providing the highest precision and thus optimal work results. It has been constructed using 3D simulations and FEM analysis to increase efficiency. All flat guides of the machining center are hand-scraped and polished. The manufacturer’s over 60 years of machine-building experience comes into play, especially in this very time-intensive process. Even with complex heavy machining tasks, the flat guides processed in this way exhibit significantly less vibration, ensuring greater stability for higher precision and longer service life.
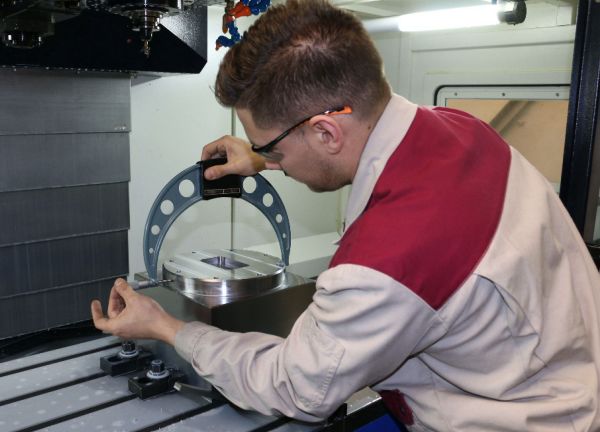
The two-speed automatic transmission spindle is – along with many other key components – not a supplier product but manufactured by Hwacheon itself. It provides high torque cutting performance at low speeds and outstanding spindle performance at high speeds. The motor is integrated directly into the high-performance spindle, ensuring stability and precision in high-speed cutting.
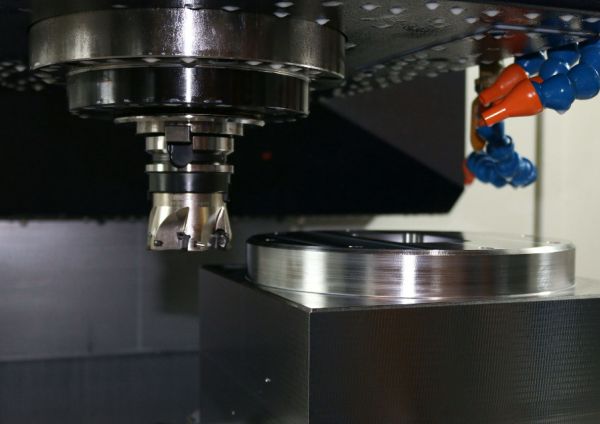
“The machine offers high rigidity primarily due to the flat guides, which also increases the accuracy of the machining,” emphasizes Nebojsa Babic. Ultimately, he was convinced by the test machining of workpieces from his area, where the machine was able to prove its performance. The quick service and uncomplicated spare parts procurement also factored into the decision.
Uniform Machine Control
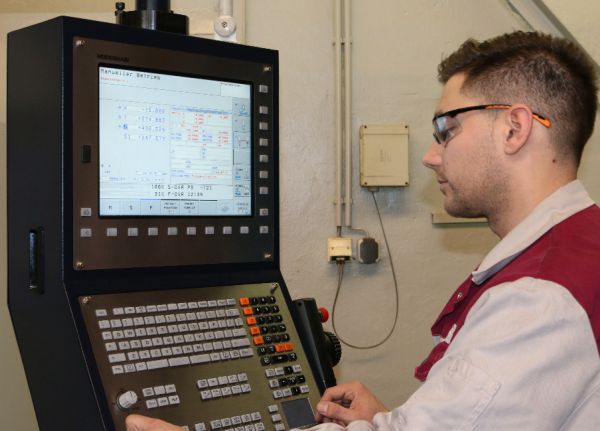
At the request of the department manager, the VESTA-1050B for TS Technology + Service was equipped with a Heidenhain control system. This allowed it to be well integrated into production, as all of the company's machines are uniformly equipped with this control system. This allows operators to switch quickly between all existing machines without having to familiarize themselves with other control systems.
In August 2016, the new milling center in Mülheim was put into operation. The employees in the machining technology department received an introduction to the machine by Hwacheon customer service. Extensive training was not required here, as the machine control system was sufficiently known.
Precise and Powerful
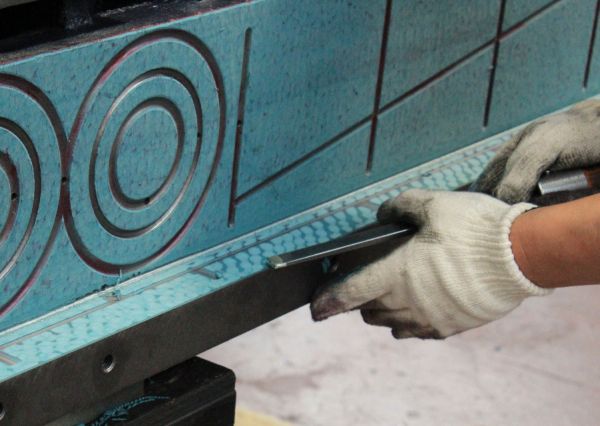
The milling center has now been in operation for more than half a year and has proven itself in the company's daily production routine. On the machine, for example, adapter plates are manufactured that are used in the reworking of large drill rods for mining. “In doing so, we have to achieve a surface better than Rz 6.3,” explains Nebojsa Babic. “The pin diameter is 220 h6 with a tolerance of 0/-0.029 mm. Thanks to the high positioning accuracy of the machine, we can achieve this fit in just two work steps.”
Marco Bock, master in machining, is also particularly impressed by the performance and robustness of the Hwacheon VESTA-1050B: “This machine has enormous power. For example, when roughing an adapter from steel in 42CrMov4, we machine at cutting speeds of Vc = 240 m/min and with a tooth feed of 0.5 mm/min, as well as when finishing the surfaces with Vc = 270 m/min and a tooth feed of 0.2 mm/min without the machine vibrating or chatter marks appearing on the workpiece.”
The great stability and robustness of the machining center ensure high availability and quality even in multi-shift operation. TS Technology + Service GmbH particularly values this, as it enables them to guarantee their customers high-quality and on-time machining of their complex precision parts and assemblies.
Mühlheim a.d.R. 45468
Germany