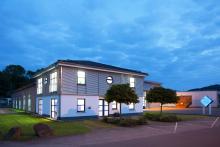
The machining of long and heavy rotational parts is particularly demanding when high precision with tight tolerances is required. This not only depends on the operator’s technical expertise, but also on the lathe being capable of meeting the high demands of machining large and heavy workpieces. To manufacture even small and very small batch sizes economically and precisely, Sauerland-based Hyss Metallbearbeitung has been successfully using large lathes from a South Korean machine tool manufacturer for many years.
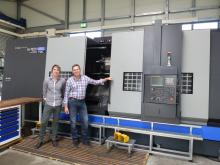
Located in the Sachtleben industrial area in Lennestadt-Meggen, Hyss Metallbearbeitung GmbH & Co. KG has a production area of 1,000 m². Here, components, welded and cast parts are manufactured for machinery, plant, and special machine construction, as well as for toolmaking, hydraulics, pneumatics, the automotive industry, and agricultural machinery. Additionally, the company offers repairs of defective components, machines, welded or cast parts, as well as shafts and bearings. If needed, defective machine parts can also be newly manufactured based on samples.
Large parts as a market niche
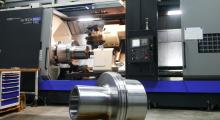
The Sauerland-based contract manufacturer specializes in machining large and heavy turned parts, welded and cast parts up to a weight of 8 tons, a diameter of 1,100 mm, and a length of 3,500 mm. Often these are custom-made or small series with low quantities. Managing Director Gerhard Hyss systematically developed this market niche. In 1982, he started out independently with two partners producing small turned parts — but that was hardly profitable. So, they decided to invest in a new area: “We wanted to produce larger parts and decided to acquire machines capable of handling diameters up to 550 mm and peak weights of 1.5 tons,” recalls Gerhard Hyss. “This allowed us to expand our service offerings and tap into new market segments.”
The concept worked, and more and more orders for large precision-turned parts came in, pushing the existing production space to its limits. As a result, a new production facility was built in 1999 at the current location. The new halls provided room for even larger machines, allowing for the machining of even larger and heavier workpieces.
First lathe from Hwacheon
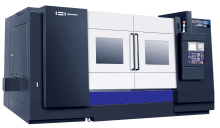
At the Metav 2002 in Düsseldorf, Gerhard Hyss came across the Hi-TECH 700 at the booth of Korean machine tool manufacturer Hwacheon. It’s a horizontal turning center for heavy-duty machining, offering an extremely rigid spindle design. The high-precision cylindrical roller bearings and shock-resistant angular contact bearings of the spindle headstock are specially designed for hard turning operations. Via the gearbox, torques of up to 3,071 Nm at 115 rpm can be achieved. Gerhard Hyss was immediately impressed by the extremely stable and well-built XL-format lathe and decided, after some market comparisons, to purchase his first Korean machine: “With the Hi-TECH 700, new doors opened for us. We could now also machine parts up to 700 mm in diameter and 2,000 mm in turning length, gaining more flexibility and speed in production.”
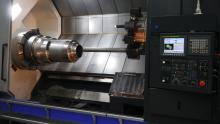
The new machine also brought in new orders for even larger workpieces. The company had found its niche and simultaneously earned a reputation as a specialist in large-part production for machinery and plant construction. As the order volume continued to grow, another Hi-TECH 700 was added in 2007 to expand production capacity. Given the excellent experience with the first machine, “it was clear,” says Gerhard Hyss, “that the next machine also had to come from Hwacheon.”
New opportunities
As the company continued to grow and storage space for raw materials became insufficient, an additional hall was built on the company premises in 2012, offering not only storage space but also room for more machines. At the same time, the contract manufacturer increasingly received inquiries for turned parts with integrated milling operations. Therefore, the acquisition of a turning-milling center was planned.
Steffen Hyss, son of the company founder and now co-managing director, saw the turning-milling center Hi-TECH 850L YMC during the opening of Hwacheon’s European headquarters in Bochum. This XXL machine can precisely process workpieces up to 8 tons in weight, 920 mm in diameter, and 3,500 mm in turning length. In addition to traditional turning, the combination with a Y-axis allows milling operations in a single setup. This increases precision, as clamping errors from switching between turning and milling machines are eliminated. The junior manager and his colleague were so impressed with the combination machining and high flexibility that the company decided to invest in this machine.
Extremely rigid machine bed and flat guides
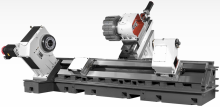
The sturdy and robust machine features an exceptionally rigid monolithic machine bed weighing 23.5 tons, produced in Hwacheon’s own foundry. For optimal thermal management, it is angled at 45 degrees to ensure hot chips are reliably removed. This prevents excessive heating of the machine and workpiece even during rough machining with high chip volumes. All flat guides are hand-scraped and polished. This time-consuming process clearly reflects the manufacturer's over 60 years of machine-building expertise. Even under heavy-duty machining, the flat guides exhibit significantly less vibration, ensuring greater stability, higher precision, and longer tool life.
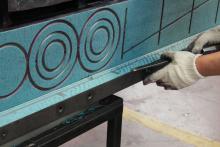
The massive double turret, with a width of 250 mm, allows for the stable clamping of large boring bars up to 80 mm in diameter and 1,000 mm in turning length. The four-speed main spindle gearbox provides exceptionally high torque, especially in the lower speed range. Lubrication and cooling of the bearings are handled by Hwacheon’s specially developed oil cooling system. The temperature of the two-stage gearbox is continuously regulated to minimize thermal expansion, ensuring machining accuracy during prolonged use and heavy cutting. With a drive power of 45 kW, the machine reaches a maximum torque of 6,873 Nm.
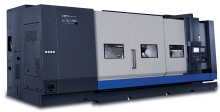
Machining technician Andreas Schöttler is thrilled with this immense power: he has never had to run the machine at full load. “Due to our small batch and single-part production, the quality and precision of the machined components are very important to us. We don’t need to run at full capacity to achieve faster machining. For individual parts, it’s not about saving a minute; it’s about quality.” On the HiTech 850, the company has successfully machined all materials from structural steels, pre-hardened steels, tempered steels, stainless steels, and brass to plastics and super duplex steels. “Thanks to the powerful drives and generously dimensioned flat guides, we consistently achieve high-quality parts with the HiTech 850,” adds Steffen Hyss. The family-owned company is particularly proud that with their machine park they can achieve a precision of up to 1/100 mm and a complaint rate close to zero.
High availability
For two years now, the Hwacheon Hi-TECH 850L YMC has been in daily use at Hyss Metallbearbeitung without any significant downtime, and the two older machines also continue to operate reliably. Gerhard and Steffen Hyss are so satisfied with the quality and precision of these machines that they have since added another Hwacheon lathe, the smaller Hi-TECH 450C, to their operation. Furthermore, the company in Lennestadt is currently considering investing in a machining center from the same manufacturer. The growth of this Sauerland-based contract manufacturer specializing in large parts is far from over.