Innovations for Tomorrow's Manufacturing Technology
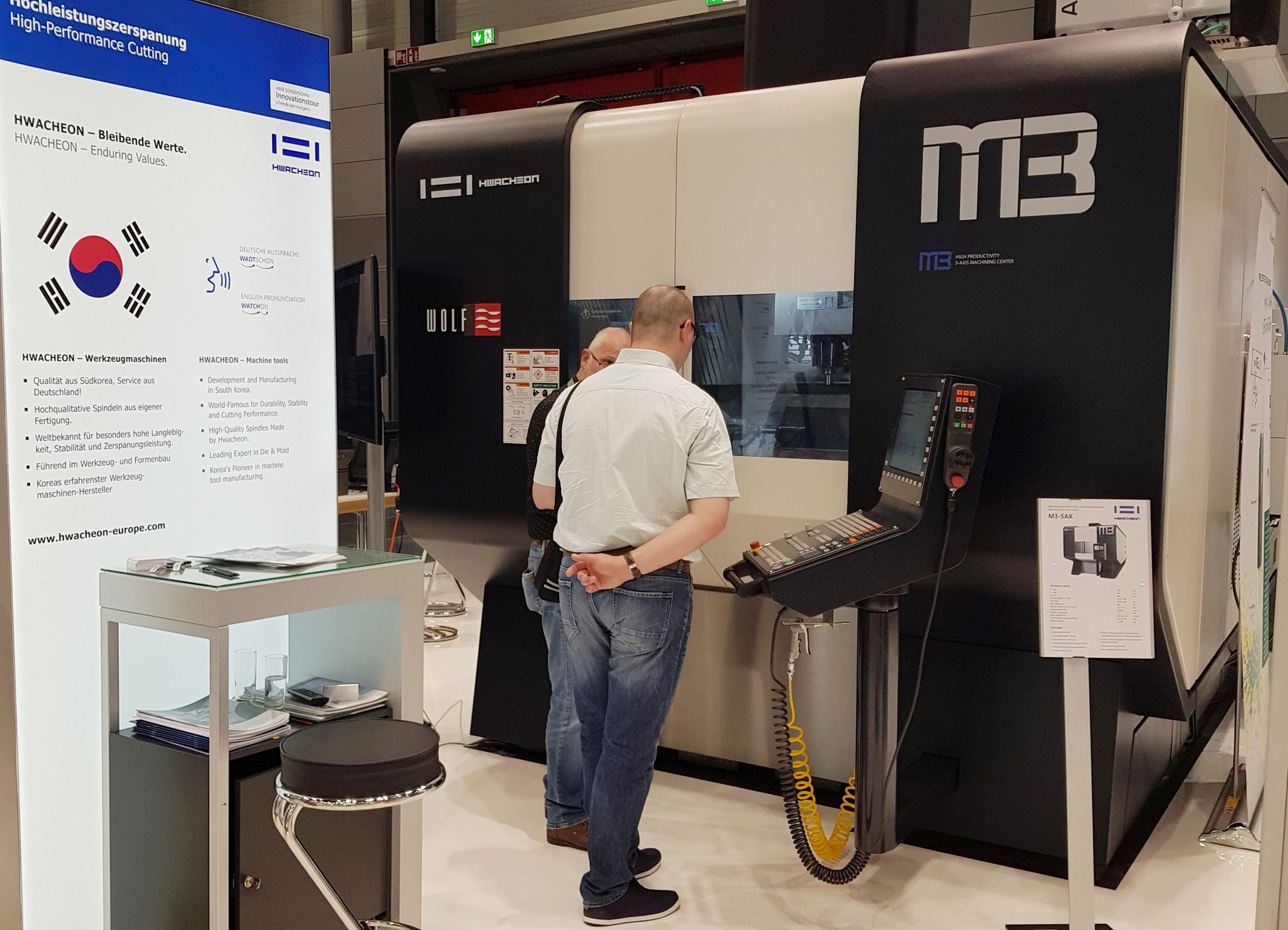
During this year's AMB in Stuttgart, the newly opened Paul Horn Hall hosted the "Innovation Tour Metalworking" special exhibition by the Institute for Production Management, Technology, and Machine Tools (PTW) of TU Darmstadt.
Special Exhibition “Innovation Tour Metalworking” by TU Darmstadt
Under the mottos “Be part of tomorrow's trends” and “Manufacturing technology of tomorrow,” trend-setting new developments were presented in various thematic clusters, with which the industry's innovation leaders are already responding to the challenges of tomorrow's machining.
- More info: M3-5AX
Process-Secure Machining

The "High-Performance Machining" cluster focused on the machining of hard and challenging materials. The interplay between machine tool, tool, CAM path planning, process monitoring, and quality assurance was demonstrated live under realistic conditions. The PTW institute of TU Darmstadt showcased spiral gearing according to Gleason in 30CrNiMo8V material on the 5-axis machining center M3-5AX from industrial partner Hwacheon. The machine tool consistently achieved an impressive surface roughness of Ra > 0.4 µm on the gear flanks, documented by measurement protocols.
The innovative M3 with a 700 mm rotary table and linear-guided 5-axis simultaneous machining in gantry design features twin drives in the A- and Y-axis. Travel speeds of 48 m/min and directly driven, oil-cooled spindles with up to 37 kW drive power at 303 Nm ensure high productivity and stable processes. Magazines with 40, 60, or even 90 slots allow for the shortest changeover times when machining workpieces with a high demand for different tools, reducing production times and costs. The 21 t heavy machine bed made of Meehanite cast iron, and direct path measurement systems in all axes ensure high precision even in hard-to-machine materials.
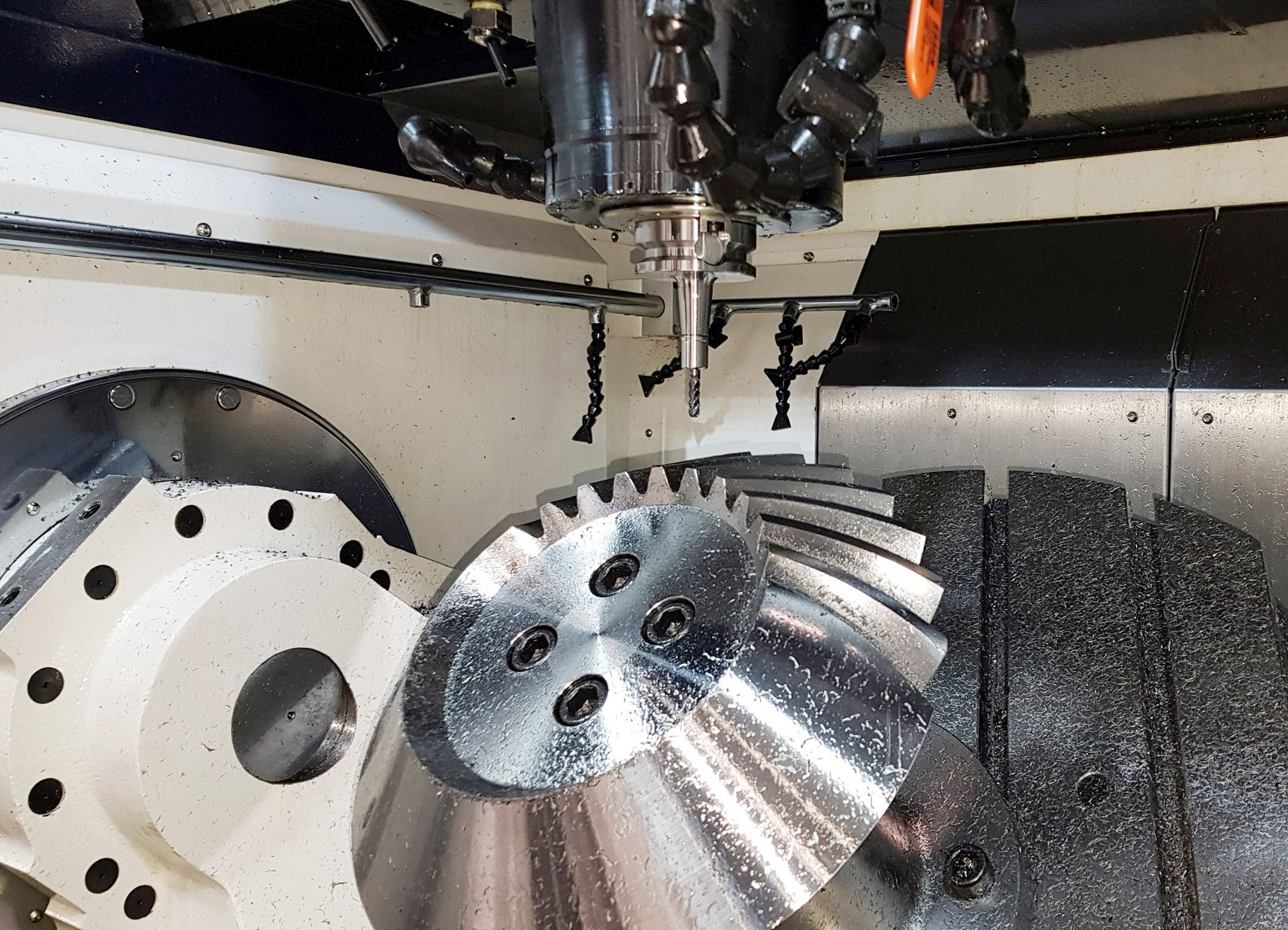
For machining demanding workpieces, the M3-5AX was equipped with special milling tools and additional components. Innovative CAM software was used for path planning for heavy-duty machining. In addition, the machine was equipped with minimal quantity lubrication operating at 12 bar pressure, demonstrating impressive performance, especially in deep hole drilling. By bundling these components into one machining center, stand visitors were given an impressive outlook on tomorrow's manufacturing technology while being convinced of the performance and precision of the South Korean brand manufacturer of robust and durable machine tools.