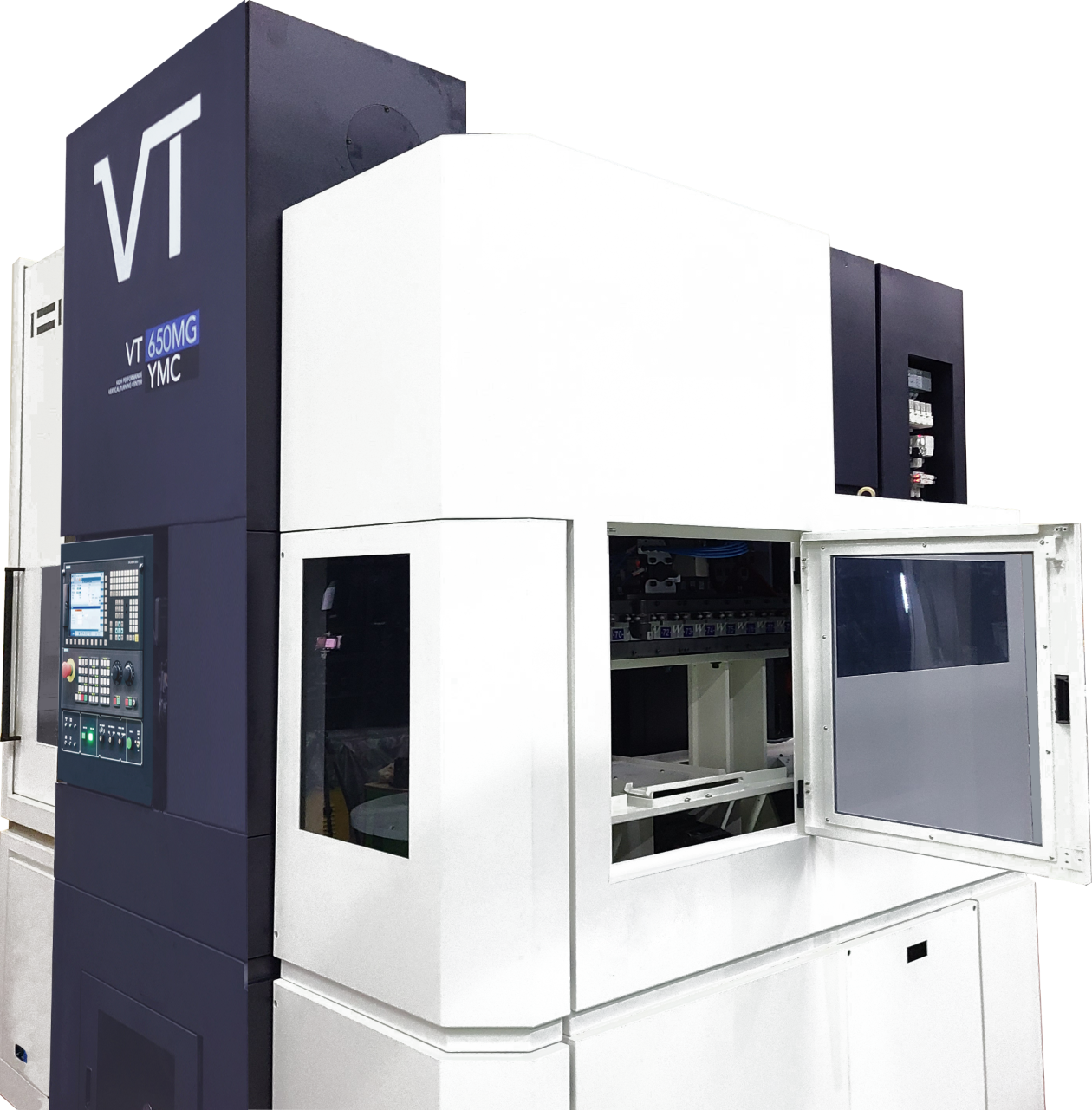
HWACHEON is one of South Korea’s most traditional machine tool manufacturers. Since 1952, we have been producing in our domestic plants and are thus the oldest manufacturer of turning and milling machines in the country. As early as 1977, the company pioneered future-oriented machining technology with the first Korean NC lathe and has continued to expand its technological leadership over the decades — to this day.
Tradition and innovation are not mutually exclusive, and we consciously maintain time-tested practices — in the interest of our customers: convinced of their reliability, precision, and durability, we continue to rely on hand-scraped flat guides made with the greatest care, heavy cast beds, state-of-the-art spindle technology — all in-house production and proudly “Made in Korea.”
In 2019 and 2020, we introduced numerous highlights and expanded our product lineup with additional models.
Vertical Lathes with Y-Axis
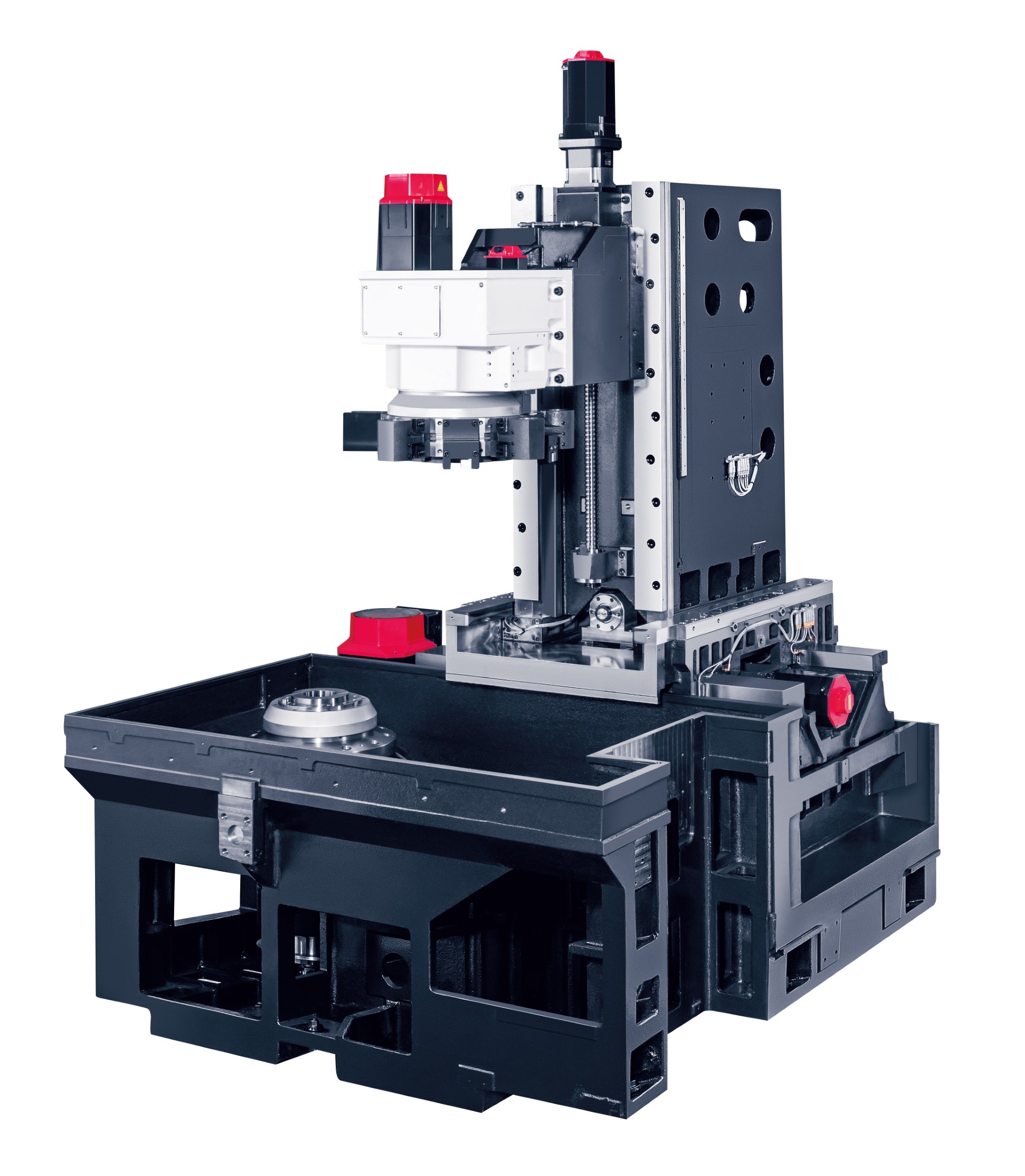
The five-model VT series is in continuous use at many globally renowned companies and is one of our most successful series, particularly in Europe. Despite often harsh operating conditions, the vertical lathes impress with their precision and reliability. For this reason, they are widely used in automated production lines, especially where hard-to-machine materials are involved.
To meet the demand for vertical lathes that can be easily integrated into production lines for complex workpieces — covering both turning and milling operations — we recently released a revised version of our VT-650.
Since the summer of this year, the VT-650 has been available with a Y-axis (±125 mm). As per our tradition, we continue to use flat guides on all axes to ensure maximum stability and durability.
Expansion of the Hi-TECH Series
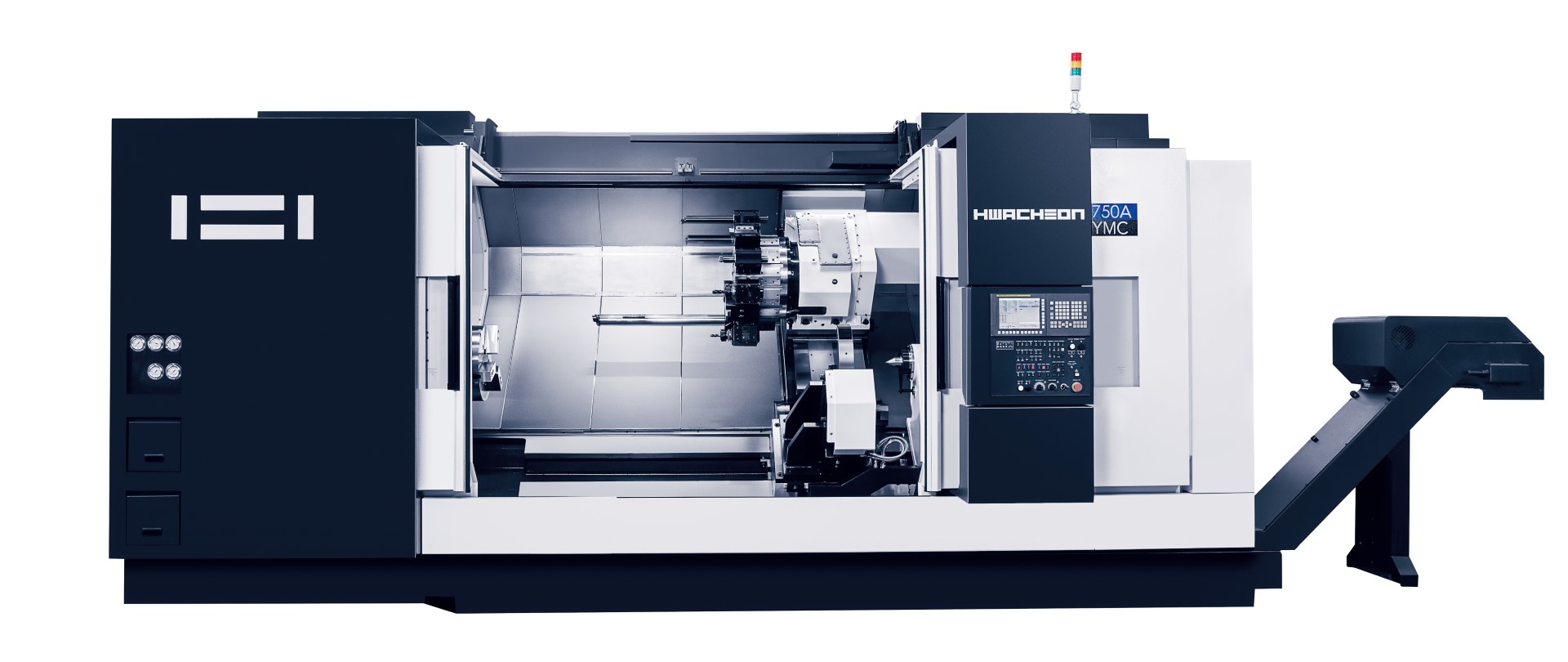
At the turn of the year, we expanded the flat-guide horizontal lathe series with another heavyweight. The new Hi-TECH 750 handles turning diameters of up to 760 mm and is available in three different bed lengths (2 / 3 / 4 meters).
Numerous optimizations have been made, especially in terms of stability. The dual-row BMT85 turret — included as standard — allows tools to be mounted with two holders per station. This provides excellent support for particularly long tools used in drilling and internal machining, significantly reducing vibration.

Many optimizations were also made to the spindle headstock housing the two-stage gearbox. We increased the bearing diameter to 240 mm to withstand high loads in continuous operation. Lubrication and cooling with temperature monitoring are handled by a specially developed system in which an oil-based aerosol flows through the bearings and gearbox for optimal supply.
The one-piece machine bed of our Hi-TECH 750, made from Meehanite cast iron, absorbs vibrations extremely well and weighs an impressive 22 tons even in the smallest 2-meter version.
Available with Siemens and Fanuc controls and numerous configuration options, it is ideally suited for large workpieces and demanding alloys.
New Automation Solutions for Machining Centers
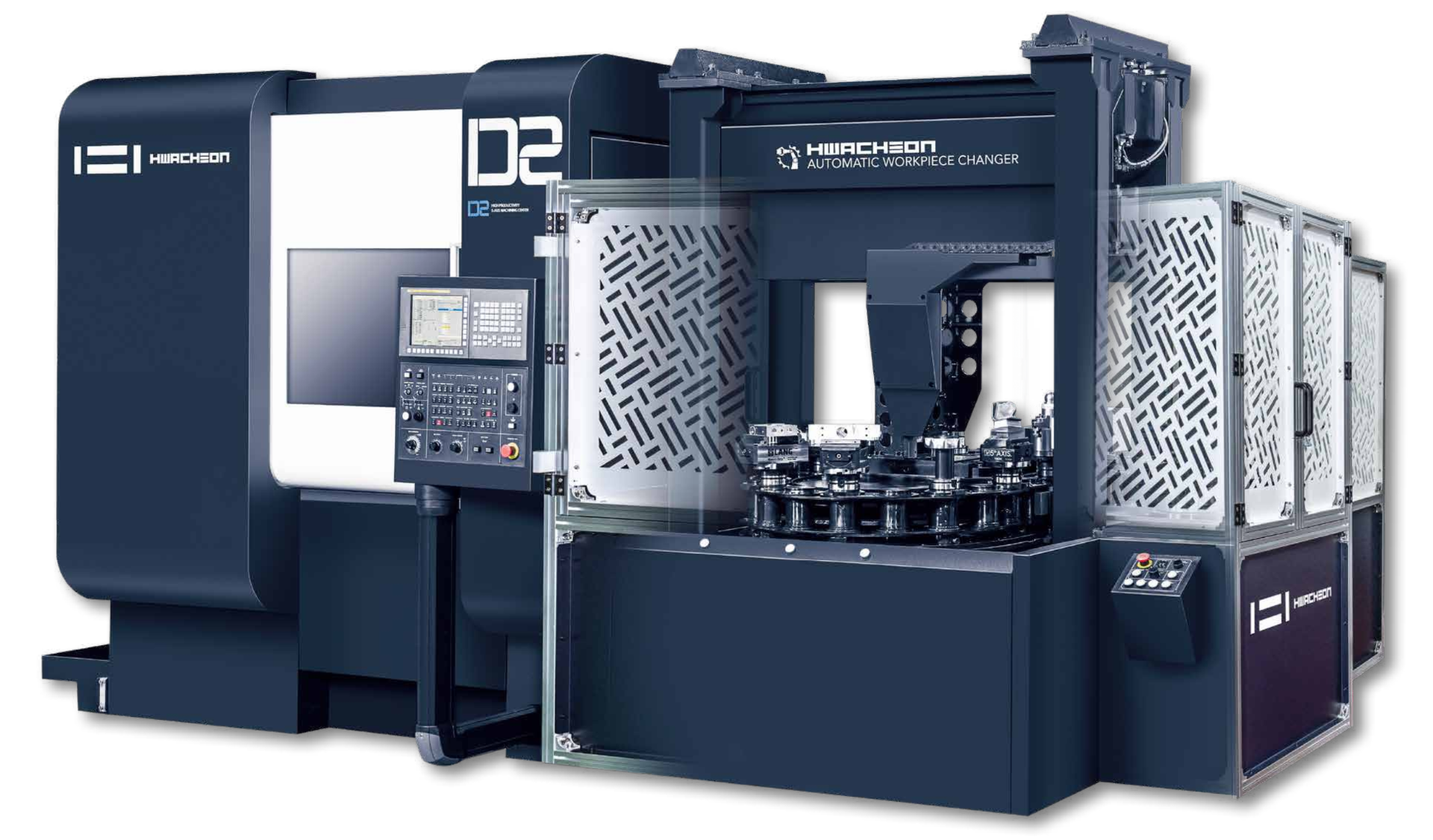
The parent plant in Gwangju, Korea, has also impressed with two new series of cost-effective automation solutions for milling machines.
The new HMP series is an automation solution for machining centers that enables fully automatic loading and unloading of pallets with standard market formats weighing up to 2 tons. The rack-style pallet pool, whose capacity can be individually adjusted, enables automation for one or even two machines.
For smaller workpieces up to 300 mm in diameter and 80 kg in weight, the AWC series (Automatic Workpiece Changer) is now available, built in two sizes with 8 or 20 magazine slots. Loading takes place from the side via a linear robot through an automatically opening partition. HSK-T100 holders are used to clamp workpieces, which are secured via vices, screw connections, or other clamping systems. Manual or crane-assisted loading and unloading occurs at the front-accessible setup station.
Both new developments are available for almost all machining centers and can also be retrofitted to older machines.